正如精益和丰田生产系统(TPS)一样, 模块化设计正迅速成为工程界的“行话”。 将其纳入业务可能带来很多好处,但同时它可能有缺点。 通常,模块化的价值大大超过了标准化产品线可能带来的任何问题。 然而,往往很难在模块化开发过程当中完全实现所有可能的价值或好处。
无论如何, 标准化零件和组件似乎是一项艰巨的任务,但你必须从某个地方开始。下面以雷蒙企业的应用为例,为大家解释模块化设计的基本概念。
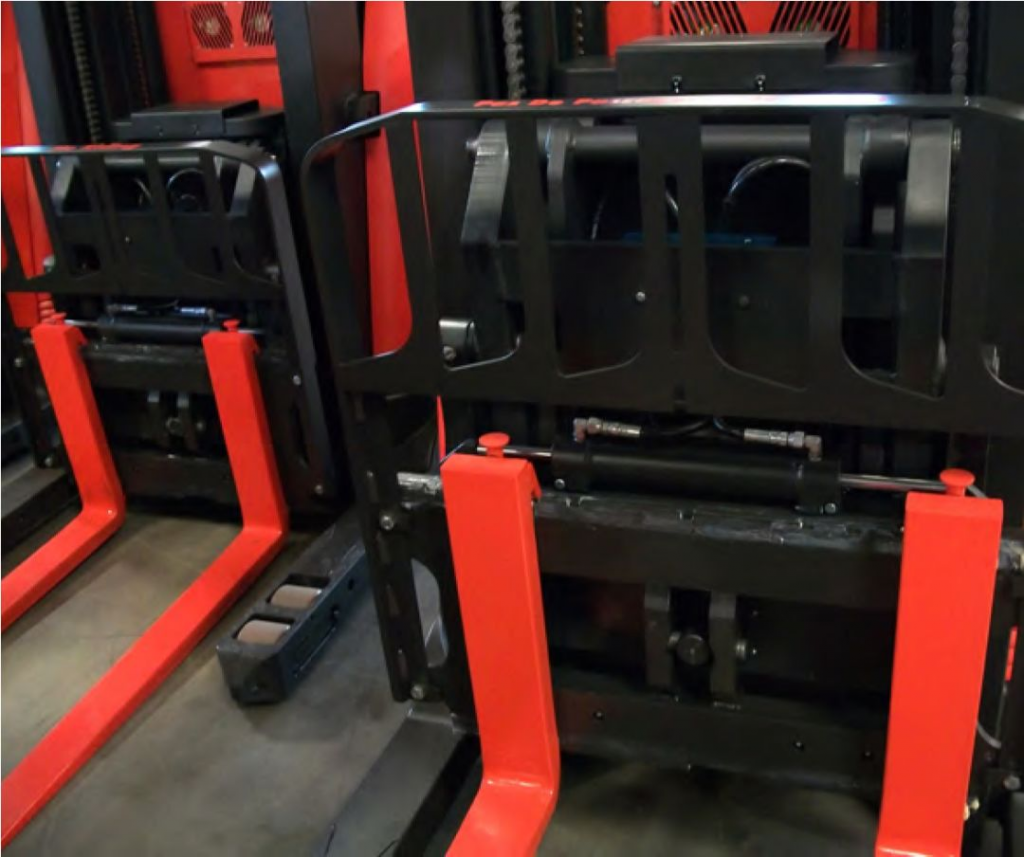
这家企业为丰田物料搬运北美集团设计,建造和销售物料搬运设备。他们与丰田联系紧密,是他们文化的重要组成部分。为了优化流程,他们正进行模块化发展。已经有几个子组件标准化项目可以应用在多个产品线上。
在仓储业务中,雷蒙公司针对不同应用设定特定要求。例如,他们有大约10个不同的产品系列,每个特定产品系列有8个型号,每个型号有5个重量级别,每个重量级别有86种不同的高度范围。这只是他们现有配置的复杂性的一瞥,实际情况往往更惊人。从行外人的角度出发,这可能看起来很荒谬,但它确实可以满足客户的特定需求和要求。 大规模定制便是雷蒙公司的业务特质。
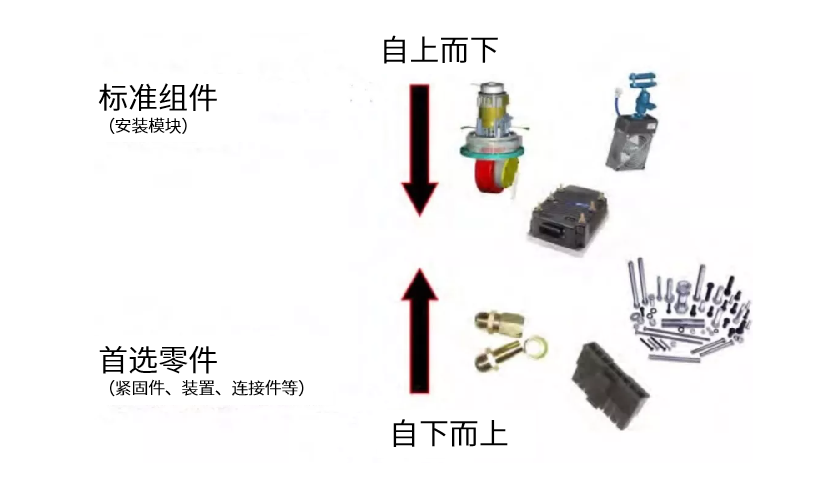
自下而上的模块化紧固件、端子、配件等……大多数OEM拥有大量的零件号,需要分配专门资源进行购买,储存,跟踪,分类和分发。 所有这些过程都会产生巨大的成本,更不用说设计人员还需要为他们的设计选择正确的硬件。
如何在这里削减成本?答案是: 自下而上的模块化。这是一种从源头上降低成本的方法: 较少的零件数等于较少的成本。他们通过检视己发布的零件并选出“首选零件”。他们拥有大量标准零件,如紧固件、液压配件、软管和其他零件等。 随着技术的发展和业务的增长,跟踪这些零件越发艰难。尽管他们采用了产品数据管理系统(PDM)来整理和跟踪这些零件以简化业务, 可随着公司不断扩大和合并其他业务实体,PDM已经难以寻找到特定的部件。
为此,他们开发PDM查询软件,以减少搜索零件的时间。 查询的结果还将告知设计人员哪些是首选零件,藉此措施以限制零件的最低库存量并增加首选零件的数量,以便采购更具杠杆作用。标准化组装接口可是另一项有益的举措。自上而下的模块化涉及在完成的产品上指定子组件之间的特定接口。这是目前汽车等大型工业的常见做法。新车中的大多数选项都是很好的模块化例子。它们用于多种不同的车型;车辆可以容纳多个不同的模块,以创建大量的定制选项而无需繁琐的工作。这种设计思路也可以使小公司受益匪浅。
将受控模块纳入开发工程有很多原因,除了制造之外,还可能节省开支。增加子组件的单量,在多个产品线上使用,可以降低成本。随着单量的增加,便可用于更精简、更高效的工艺生产零件。
减少零件数是这一过程的自然结果,降低了管理和库存成本。利用组件的标准接口还可以通过增加和移除模块来提高满足客户需求的灵活性。这些标准模块亦能加快包含这类标准模块和接口的新品设计时间。将自上而下的模块化引入组织虽具挑战,但如果部署得当,效益将非常明显。如果模块化是一项重要战术,那么接口便是成功的关键。
正确的接口思路是自上而下模块化的最关键因素。如果所选接口不能在各种应用中使用,那组件便失去其作为模块的价值。一旦选择了接口,就需要严格控制它的生命周期。需要特别注意的是如何构建文档。
下图显示了一个螺栓圆圈被指定为受控接口,提醒人们需要彻底评估任何设计变更。
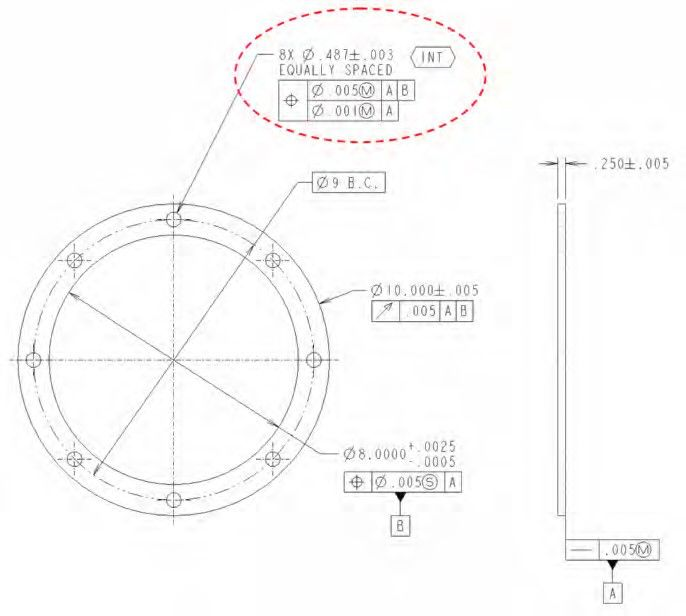
这会涉及接口规范图纸和其他模块控制文档(参见下面分层)。
接口规范的其他注意事项包括CAD结构,以及针对模块的工程更改流程。
Level 0 –
成品接口规范图
Level 1
接口规范图
Level 2
接口规范图
Level 3
接口规范图
BDI DFMA®软件对模块化开发方面非常有用。模块的主要目的是增加数量,从而降低成本。在开发阶段使用DFMA®软件优化模块的设计以控制成本对于模块的成功是非常有利的。
通常,特定的模块需要满足多个产品线的要求。例如,一个入门级产品与高级产品使用相同的子组件。这种模块化原则有时很难令人接受,那怕是模块已经进行了全面的成本评估,并将成本最小化。优化好的模块比部分成本的累加有更大的节省空间,以及简单而可靠流程的增值点,这都是难以言明的。DFMA®软件帮助雷蒙企业成功推行模块化。
DFMA®软件让工程师有能力在设计早期阶段预估成本,引导更好的设计决策。下图展示出DFM和DFA在模块化项目中那个时候起作用:
设计要求和接口研究
设计概念
制造可行性评估
DFMA®评估
接口评估
制造专家和管理层设计评审
概念选择
在设计过程早期让制造部门和专家参与进来可以加快项目进度。共享DFMA®结果可以减少工程师的假设并产生同步的成本估算,生成更可靠的数据以做出最佳决策。DFMA®在模块开发项目中,确保所有关键人之间的良好沟通至关重要。雷蒙德公司利用上述过程将负载稳定焊件不同的变种(参见下图)简化为模块化和可适性的设计。
这需要研究相关的产品和接口要求并生成多个设计概念。之后,使用DFM工具分析每个设计概念,并与制造和设计工程的代表一起审查结果和概念。选择好概念后并开始正式的设计工作,这包括模块化文档定义和界面约束条件。
结果展示出最初的12个不同系列的负载靠背(LBR)焊件可以简化为三个模块化的系列设计,并共享共同的零件。新型负载靠背旨在利用简单、可重复的制造工艺。该设计理念还允许机器人焊接夹具适应未来的尺寸变更,从而在模块生命周期内为所有未来和当前产品创建标准组件。
通常,特定的模块需要满足多个产品线的要求。例如,一个入门级产品与高级产品使用相同的子组件。这种模块化原则有时很难令人接受,那怕是模块已经进行了全面的成本评估,并将成本最小化。优化好的模块比部分成本的累加有更大的节省空间,以及简单而可靠流程的增值点,这都是难以言明的。DFMA®软件帮助雷蒙企业成功推行模块化。
DFMA®软件让工程师有能力在设计早期阶段预估成本,引导更好的设计决策。下图展示出DFM和DFA在模块化项目中那个时候起作用:设计要求和接口研究设计概念制造可行性评估DFMA®评估接口评估制造专家和管理层设计评审概念选择在设计过程早期让制造部门和专家参与进来可以加快项目进度。共享DFMA®结果可以减少工程师的假设并产生同步的成本估算,生成更可靠的数据以做出最佳决策。DFMA®在模块开发项目中,确保所有关键人之间的良好沟通至关重要。
雷蒙德公司利用上述过程将负载稳定焊件不同的变种(参见下图)简化为模块化和可适性的设计。
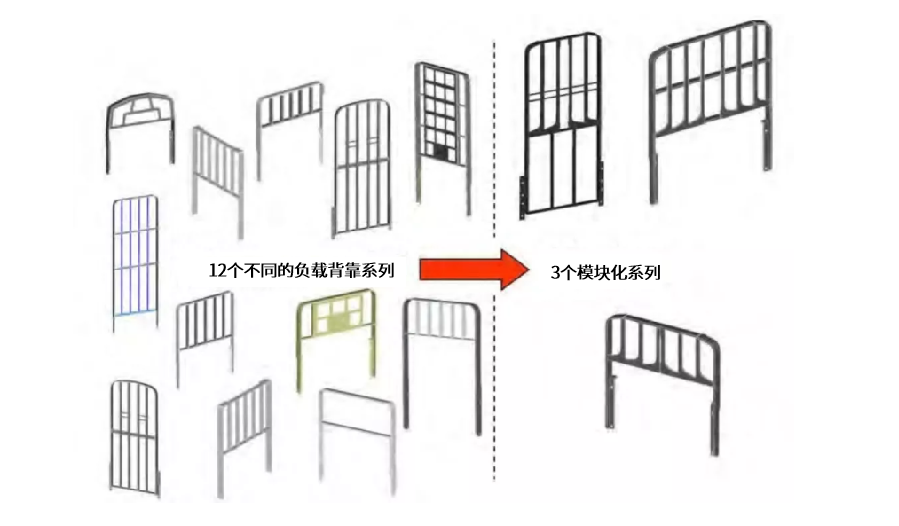
这需要研究相关的产品和接口要求并生成多个设计概念。之后,使用DFM工具分析每个设计概念,并与制造和设计工程的代表一起审查结果和概念。选择好概念后并开始正式的设计工作,这包括模块化文档定义和界面约束条件。
结果展示出最初的12个不同系列的负载靠背(LBR)焊件可以简化为三个模块化的系列设计,并共享共同的零件。新型负载靠背旨在利用简单、可重复的制造工艺。该设计理念还允许机器人焊接夹具适应未来的尺寸变更,从而在模块生命周期内为所有未来和当前产品创建标准组件。