索斯科(Southco)于1899年在美国宾夕法尼亚州创立,是全球领先的工程进入解决方案供应商,业务版图跨越美洲、欧洲和亚太地区,为全球70,000多家客户提供产品和服务。
索斯科提供工业应用解决方案,如锁具、紧固件、铰链/定位控制技术、电子门禁等产品,应用于船舶、汽车、工程机械/建设、轨道交通、航空航天、机箱机柜、医疗器械、工业机械、暖通空调、数据中心以及服务器设备。
改善背景
索斯科百分之三十以上的生意是定制产品。
2009年,由于某客户的定制铰链的价格预算与索斯科评估的制造成本基本等同,索斯科几乎没有任何利润。
在此情况下,索斯科必须找到一种新的方法来降低产品的总成本。DFMA®帮助索斯科实现了他们的这一愿望。
改善效果
通过使用DFMA®,产品开发团队能够极大地减少了定制铰链的装配时间和成本,并消除一些制造过程的操作。
最后使索斯科满足了客户提出的所有要求并实现了铰链盈利,同时使得铰链操作更安静且能承受更高的负荷。
改善过程
新旧铰链的设计
如下图所示:
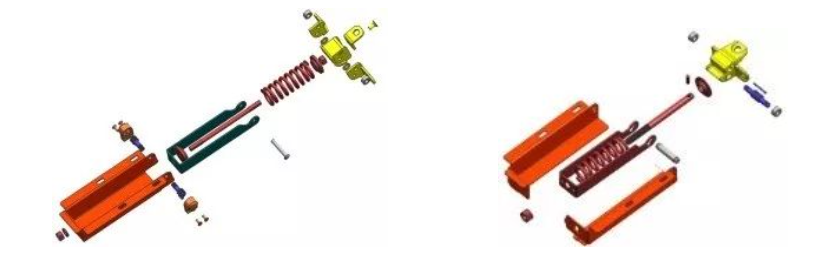
左图显示了中心壳体(右上、黄色)、铰链点(左下角、橙色)和平衡装置(中心、红色和绿色)组件。
新旧设计改善对比的效果:
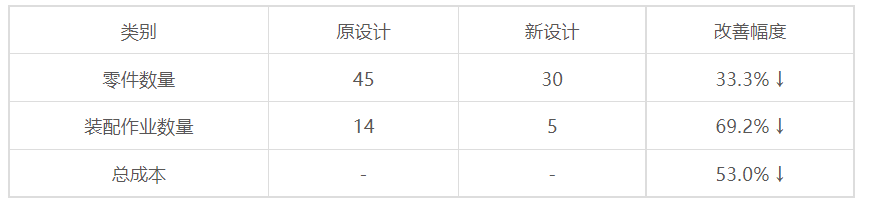
改善亮点
为了方便和简单,开发团队将他们的DFA分析分解成三个子组件:1.中心壳体。其所包含的零件见下表:
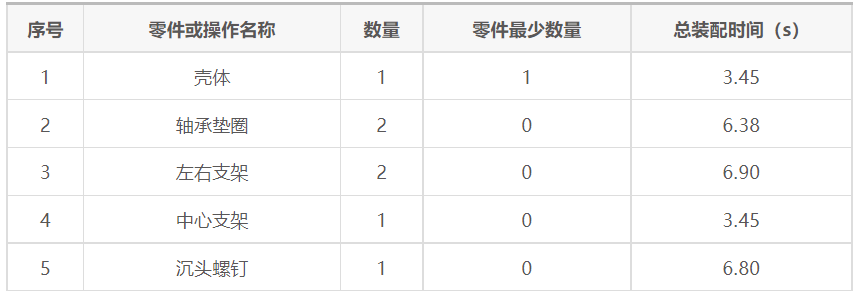
该组件位于平衡弹簧的一端。“零件最少数量”列表明,有极好的机会可以减少装配时间,特别是对于螺钉驱动和支架装配(见表二)。
新设计将支架作为单独零件,采用单件铸造。新设计降低了组件成本60%,同时也消除了三个冲压模具,一个攻丝操作,一个螺丝驱动操作,以及工具成本等。2.铰链点组件。其所包含的零件见下表:
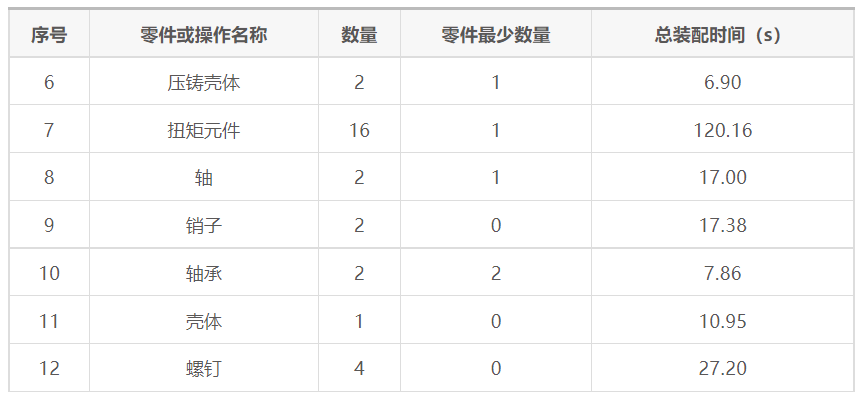
该子组件位于弹簧的另一端,包括保持铰链轴和扭矩元件在内的压铸壳体。
尽管它比中心壳体更复杂(29个零件),但是铰链点组件提供了较少的重新设计机会,因为许多部件是不受限制的(见表三)。
通过重新设计轴,新设计取消了四个紧固螺钉,切断了几个其他部件,简化了轴两端的两个压铸外壳。通过将冲压的壳体分成两个左右的部件,并在每个部件中为轴增加了挤压的壳体孔来形成更强的铰链。
新设计使该组件零件数量从29减少到23,组件总成本降低了28%,同时减少了一个压铸模具。
3.平衡装置组件。其所包含的零件见下表:
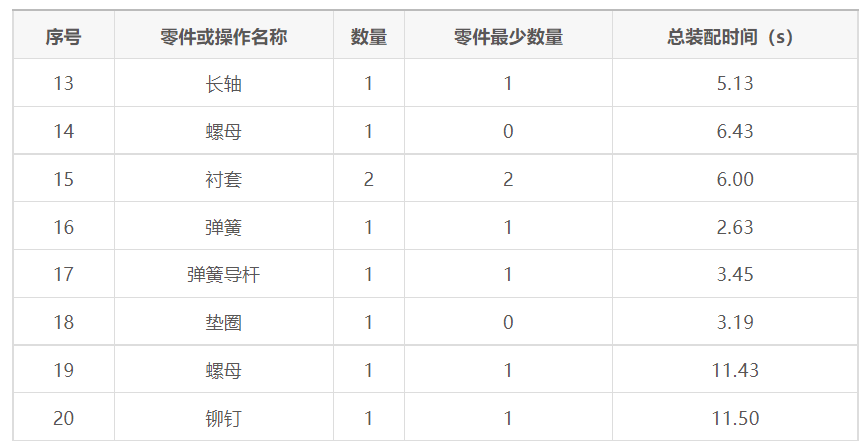
该组件提供了使外壳盖易于提升的力,尽管其重量很大。在DFA分析中,团队迅速注意到两个螺母和铆钉三个非功能部件占据了总装配时间的一半。
新设计用一个标准螺纹替换了一个定制轴。在顶端,他们通过采用与许多汽车气门机构组件相似的浮动销策略来消除螺母。通过增加一个锥形销来取代弹簧导向轮的圆孔槽铆钉。
同时增加了塑料套管解决了轴过早磨损导致吱吱声的问题。此外,按照客户要求的规格,增加了额外的弹簧(安装在原弹簧内)以支持更高的负载,以及杯状垫圈来提供对中。
最终的设计使该部件成本降低了28%,并且消除了一个铆钉锤击和一个螺母驱动操作。
改善小结
使用DFMA®设计产品让索斯科的铰链设计团队感受颇深,归纳起来有以下两点:
1.跨职能团队的设计模式让设计工程师关注产品设计更多的方面。如设计工程师过去不关注成本及产品如何能够有效制造出来,不关心产品的质量问题等。
现在通过与其他部门的工程师充分讨论,意识到了跨职能团队紧密合作进行产品开发的好处,也愿意去考虑产品功能设计之外的因素,如质量风险、工艺设置、制造成本等。
2.DFA能够快速得出产品最少零件种类和数量。通过DFA定量评估零件设计和总装配,帮助工程师快速识别不必要的零件,因为它们影响了产品的装配时间和成本。
另外它还提供了消除零件的策略。DFA再设计分析的结果是一种更简单、更可靠的产品,其功能既高效又易于组装。