铣削是最常见的加工形式,一种材料去除过程,通过切割不需要的材料,可以部分创建各种功能。铣削过程需要铣床、工作件、夹具和切割机。工作件是固定在夹具上的预形材料,它本身就连接到铣床内的平台上。切割机是一种切割工具,牙齿锋利,也固定在铣床中,并高速旋转。通过将工作件送入旋转切割机,材料以小芯片的形式从该工作件中分离,以创建所需的形状。
铣削通常用于生产非轴向对称且具有许多特征的部件,如孔、槽、口袋,甚至三维表面轮廓。完全通过铣削制造的部件通常包括数量有限的组件,可能用于原型,如定制设计的紧固件或支架。铣削的另一个应用是为其他工艺制造模料。例如,三维模具通常是碾磨的。铣削还通常用作辅助工艺,用于添加或优化使用不同工艺制造的部件的功能。由于铣削可以提供高公差和表面表面完成,因此非常适合为其基本形状已经形成的部分添加精密功能。
典型 | 可行 | |
形状: | 固体:立 方固体:复杂 | 平 薄壁:圆柱形 薄壁:立方 薄壁:复杂 实心:圆柱形 |
部分尺寸: | 长度: 0.04 – 72 宽 度: 0.04 – 72 在 | |
材料: | 金属 合金钢 碳钢 铸铁 不锈钢 铝铜 镁锌 | 陶瓷 复合材料铅 镍 锡 钛 弹性体 热塑性 塑料热集 |
表面完成 – 拉: | 32 – 125 μin | 8 – 500 μin |
容忍度: | ± 0.001 | ± 0.0005 在. |
最大墙厚度: | 0.04 – 40 在。 | 0.04 – 72 在. |
数量: | 1 – 1000 | 1 – 1000000 |
领先时间: | 日 | 小时 |
优势: | 所有材料兼 容性非常好的 公差短交前时间 | |
弊: | 有限的形状复杂 性 部分可能需要多个操作和 机器 高 设备成本 显著工具磨损 大量报废 | |
应用: | 机器部件、发动机部件 |
过程周期:
生产给定数量的零件所需的时间包括初始设置时间和每个零件的周期时间。设置时间由设置铣床、计划工具移动(无论是手动操作还是按机器执行)并将夹具设备安装到铣床中的时间组成。周期时间可分为以下四次:
1.装载/卸载时间- 将工作件装载到铣床并将其固定到夹具上所需的时间,以及卸载已完成部分所需的时间。负载时间取决于工作件的大小、重量和复杂性,以及夹具的类型。
2.切割时间– 切割机为每次操作在工作件中进行所有必要的切割所需的时间。任何给定操作的切割时间通过将该操作的总切割长度除以馈送速率(即切割机相对于工作件的速度)来计算。
3.空闲时间– 也称为非生产时间,这是在流程周期中发生的任何任务所需的时间,这些任务不会与工作件交互,因此会删除材料。此空闲时间包括工具接近和从工作件中缩回、工具在功能之间移动、调整机器设置和更换工具。
4.工具更换时间– 更换已超过其使用寿命的工具所需的时间,因此成为有效切割的磨损。此时间通常不是在每个周期中执行,而是仅在工具的使用寿命达到之后执行。在确定周期时间时,工具更换时间会根据单个部分的生产进行调整,乘以工具更换的频率,即将切割时间除以工具寿命。
在铣削过程周期之后,不需要后处理。但是,如果需要,则可用于辅助流程来改善该部分的表面完成。废料以从工作件上切下来的小型材料芯片的形式,通过切割机的移动和润滑剂的喷洒从工作件中移开。因此,无需任何工艺循环步骤即可拆卸废料,这些废料可以在生产后收集和丢弃。
切割参数
在铣削中,通过几个参数指定切割工具的速度和运动。
这些参数根据工作件材料、工具材料、工具大小等为每个操作进行选择。
切割馈送– 切割工具或工作件在主轴和工具的一次革命中前进的距离,以每转 (IPR) 英寸为单位测量。在某些操作中,工具馈入工作件,而其他操作中,工作件馈入工具。对于多点工具,切割进料也等于每颗牙齿的进料,以每颗牙齿英寸 (IPT) 为单位,乘以切割工具上的牙齿数量。
切割速度– 切割过程中工作件表面相对于切割工具边缘的速度,以每分钟表面英尺 (SFM) 测量。
主轴速度– 主轴和工具的旋转速度(每分钟革命)( RPM)。主轴速度等于除以工具周长的切割速度。
馈送速率– 切割工具相对于工作件的移动速度,因为工具进行切割。进给速率以每分钟英寸 (IPM) 为单位,是切割馈送 (IPR) 和主轴速度 (RPM) 的产物。
轴向切割深度– 工具沿着工作轴在工作件中进行切割的深度。大轴向深度的切割将需要低馈送率,否则将导致工具的高负载和减少工具寿命。因此,当工具移动到每个通路的指定轴向切割深度时,通常会在多个通道中加工一个功能。
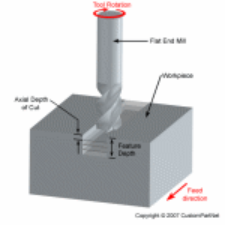
切割的半径深度– 工具在切割时沿其半径在工作件中的深度。如果切割的半径深度小于工具半径,则工具仅部分参与,并且正在进行外围切割。如果切割的径向深度等于工具直径,切割工具将完全接合,并正在进行插槽切割。大径向深度的切割将需要低馈送速率,否则将导致工具的高负载和减少工具的使用寿命。因此,当工具在跨步距离移动时,通常会分几个步骤进行一个功能,并在切割的径向深度进行另一次切割。
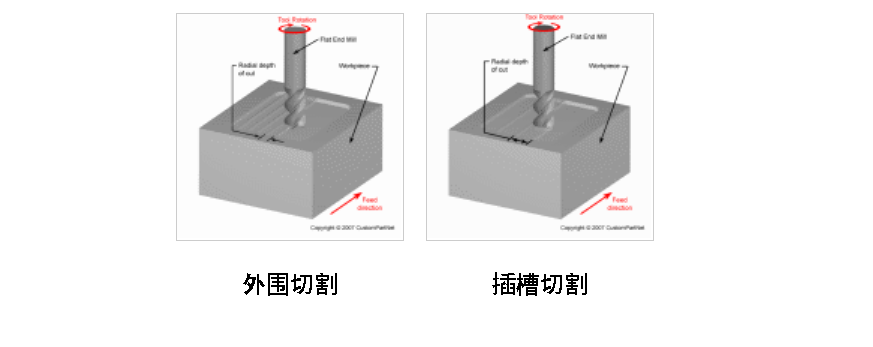
操作
在过程周期中,可以对工作件执行各种操作,以产生所需的部分形状。以下操作均由使用的切割机类型和切割机从工作件中取出材料的路径定义。
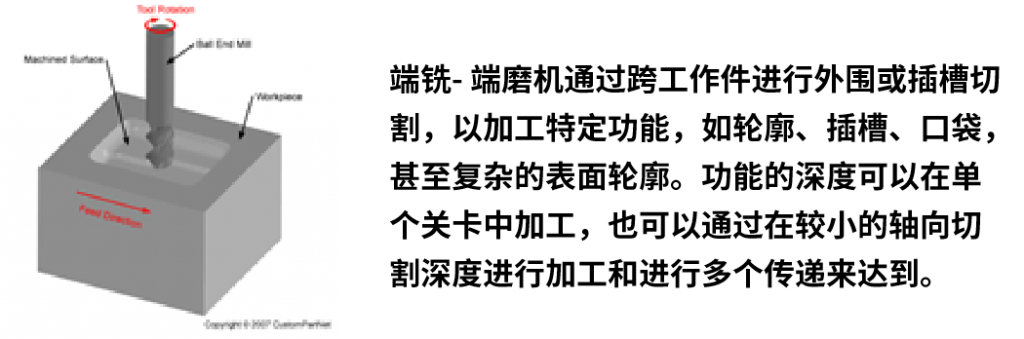
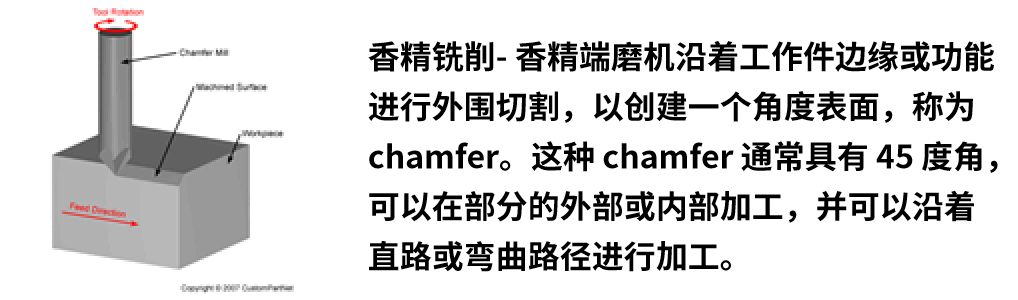
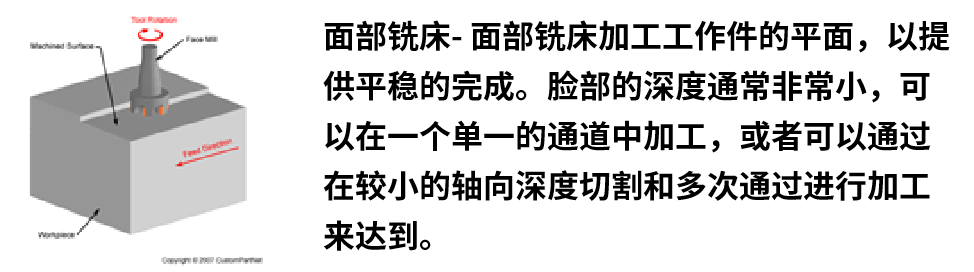
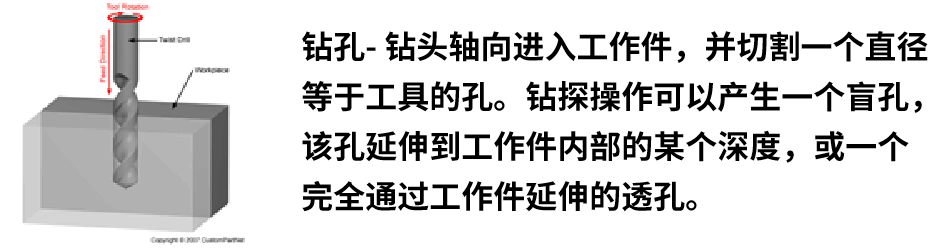

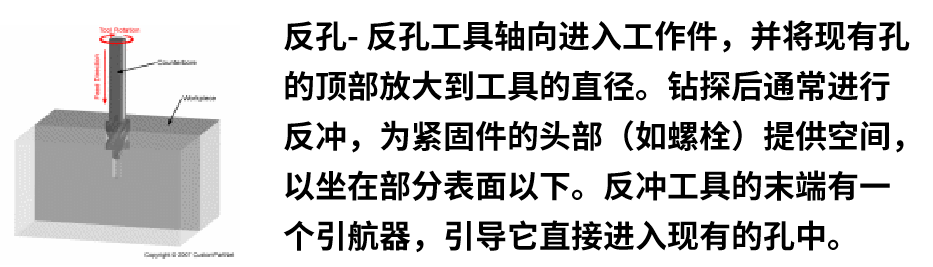
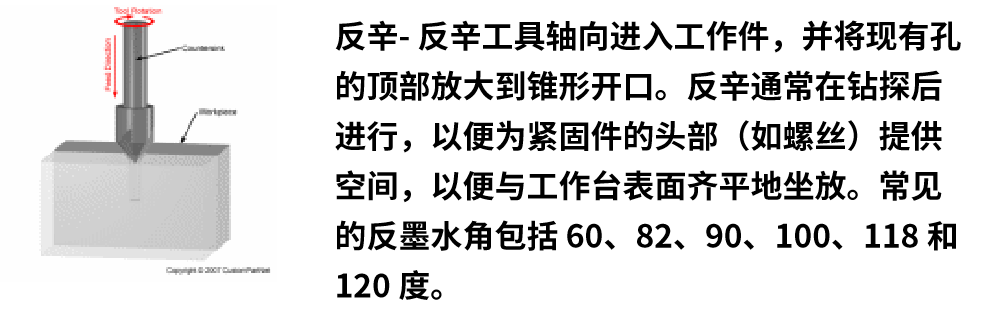

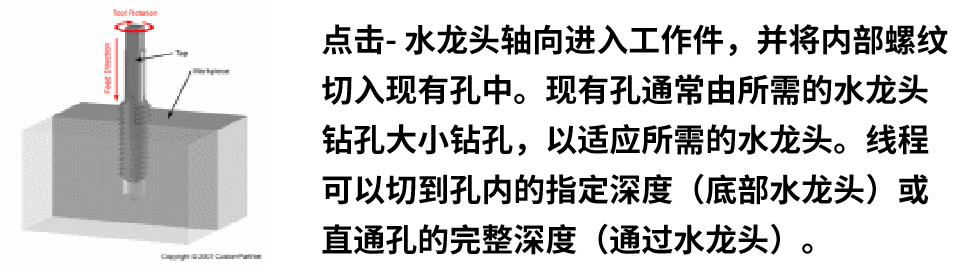
设备
铣床可以找到各种尺寸和设计,但他们仍然拥有相同的主要组件,使工作件可以移动在三个方向相对于工具。这些组件包括:
基座和柱子– 铣床的基座只是位于地面上并支撑机器的平台。大列连接到底座并连接到其他组件。
表– 将碾磨的工作件安装在称为表的平台上,该平台表面通常有”T”形槽。工作件可以固定在称为 vise 的夹具中,该装置固定在 T 槽中,或者工作件可以直接夹入这些插槽中。桌子通过沿着下面的平台(称为鞍)滑动,在 X 方向上提供工作台的水平运动。
鞍– 鞍是支撑桌子并允许其纵向运动的平台。马鞍还能够移动,并通过沿着另一个称为膝盖的平台横向滑动,在 Y 方向上提供工作件的水平运动。
膝盖– 膝盖是支撑马鞍和桌子的平台。在大多数铣床(有时称为柱子和膝盖铣床)中,膝盖提供工作件的垂直运动(Z 方向)。膝盖可以沿着柱子垂直移动,从而垂直移动工作件,而切割机则保持其上方静止。但是,在固定床机中,膝盖是固定的,而切割机垂直移动以切割工作件。
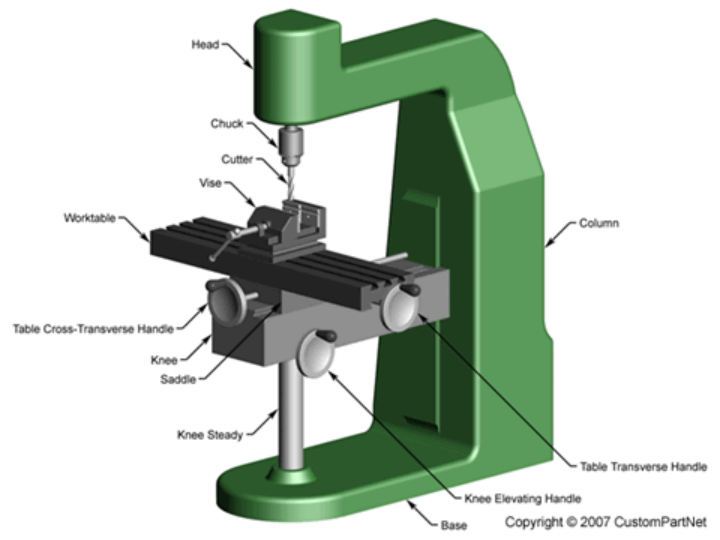
铣床的上述部件可以垂直或水平方向,形成两种截然不同的铣床形式。水平铣床使用安装在工作台上方水平轴(称为树干)上的切割机。因此,水平铣削有时被称为树干铣削。树干一侧由连接到柱子的过臂支撑,另一侧由主轴支撑。主轴由电机驱动,因此旋转树干。在铣削过程中,切割机沿水平轴旋转,切割机的侧面从工作件中取出材料。另一方面,垂直铣床将切割机垂直定向。切割机固定在一块称为小孔的碎片中,然后连接到垂直方向的主轴上。主轴位于磨削头内,铣削头附着在柱子上。在垂直铣床上进行的铣削操作使用切割机的底部和侧面去除材料。
铣床也可以按使用的控项类型进行分类。手动铣床要求操作员在铣削操作过程中控制切割机的运动。操作员使用移动桌子、马鞍和膝盖的手曲柄来调整切割机的位置。铣床也能够被计算机控制,在这种情况下,它们被称为计算机数控 (CNC) 铣床。数控铣床根据预编程并提供极高精度的命令移动工作件和切割机。编写的程序通常称为 G 代码或 NC 代码。除了标准的 X-Y-Z 运动之外,许多数控铣床还包含另一个运动轴。主轴和切割机的角度可以更改,从而可以铣削更复杂的形状。
工具
铣削所需的工具是一种由主轴旋转的锋利切割机。切割机是一种圆柱形工具,外侧有锋利的牙齿。牙齿之间的空间称为长笛,允许材料芯片远离工作件。牙齿可能沿着切割机的一侧直行,但通常排列在一个百里形中。六边形角通过分配力来减轻牙齿的负荷。此外,切割机上的牙齿数量也各不相同。更多的牙齿将提供更好的表面表面完成。可用于铣削作业的切割机种类繁多,因此可以形成各种功能。虽然这些切割机的直径、长度和切割形状差别很大,但它们也因其方向而异,无论它们是水平使用还是垂直使用。
将用于水平铣床的切割机将使牙齿沿着工具的整个长度
延伸。工具的内部将是空心的,以便它可以安装到树干上。有了这种基本形式,仍有许多不同类型的切割机可用于水平铣削,包括下面列出的切割机:飞机(螺旋)磨机、形式缓解磨坊、交错磨齿磨机、双角磨机
水平铣床也可以进行另一种称为跨层铣削的操作。这种铣削形式是指使用连接到树干并同时使用的多个切割机。跨层铣削可用于通过单个切口形成复杂功能。
对于垂直铣床,切割机的形式非常不同。切割机的牙齿只覆盖工具的一部分,而剩余的长度是光滑的表面,称为刀柄。刀柄是固定在小孔内的切割机部分,用于连接主轴。此外,许多垂直切割机设计用于使用切割机的两侧和底部切割。下面列出的是几个常见的垂直切割机:平端磨坊、球端磨坊、尚弗磨坊、面磨机、扭曲钻头、铰 刀、水龙头。
所有用于铣削的切割机都可以在各种材料中找到,这将决定切割机的特性和最适合的工作材料。这些特性包括切割机的硬度、韧性和耐磨性。使用的最常用切割机材料包括:高速钢 (HSS)、碳化物、碳钢、钴高速钢
切割机的材料是根据多种因素选择的,包括工作件的材料、成本和工具寿命。工具寿命是选择切割机时考虑的一个重要特征,因为它极大地影响了制造成本。短的工具寿命不仅需要购买额外的工具,而且每次工具磨损过多时都需要时间来更改工具。上面列出的切割机通常用不同的材料涂上牙齿,以提供额外的耐磨性,从而延长工具的使用寿命。在铣削过程中,还可以通过在切割机和工作件上喷洒润滑剂和/或冷却剂来减少工具磨损。这种液体用于降低切割机的温度,在铣削过程中会变得相当热,并减少切割机和工作件之间的接口摩擦,从而增加工具的使用寿命。此外,通过在铣削过程中喷洒液体,可以使用更高的进料率,可以改善表面表面表面,并推开材料芯片。典型的切割液包括矿物油、合成油和水溶性油。
材料
在铣削中,材料的原始形式是切割工作件的一块库存。此库存有多种形状可供选择,如平板、实心条(矩形、圆柱形、六角形等)、空心管(矩形、圆柱形等)和形状光束(I 形梁、L 形梁、T 形梁等)。有时还使用自定义挤出或现有部件(如铸件或锻件)。
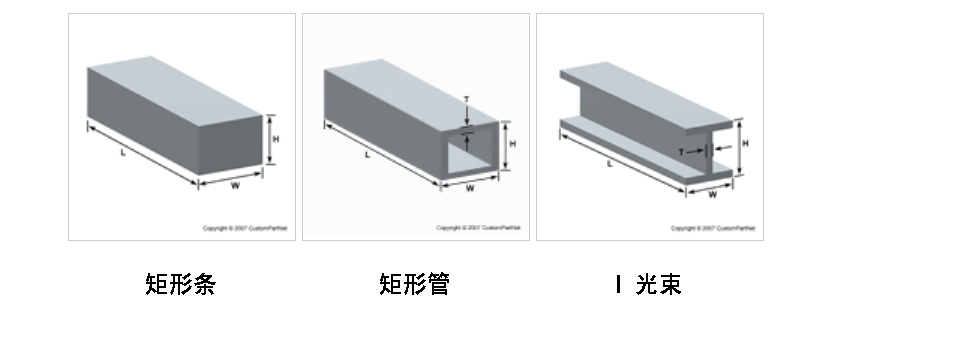
铣削可以在各种材料(包括大多数金属和塑料)的工作件上进行。用于铣削的常用材料包括:铝、黄铜、镁、镍、钢、热集塑料、钛、锌
在选择材料时,必须考虑几个因素,包括成本、强度、耐磨性和可加工性。材料的可加工性难以量化,但可以说具有以下特征:
1.结果在良好的表面完成
2.促进工具寿命长
3.需要低力和功率磨
4.提供轻松的芯片集合
可能的缺陷
铣削中的大多数缺陷都是在特征尺寸或表面粗糙度方面不准确。这些缺陷有以下几个可能的原因:
1.不正确的切割参数– 如果切割参数(如进料速率、主轴速度或轴向切割深度过高)过高,则工作件表面将比预期粗糙,并可能包含划痕甚至烧伤痕迹。此外,大深度的切割可能导致切割机的振动,并导致切口不准确。
2.杜尔切割机– 使用切割机时,牙齿会磨损并变得沉闷。沉闷的切割机制作精密切割的能力较差。
3.无担保工作件– 如果工作件在夹具中未牢固夹住,铣削摩擦可能导致其移动并改变所需的切割。
设计规则:工件
1.选择能够最大限度地降低整体成本的材料。廉价的工作件可能导致更长的切割时间和更多的工具磨损,增加总成本
2.通过预先切割接近所需尺寸和形状的工作件,最大限度地减少铣削量
3.选择工作件的大小,以便存在足够大的表面,以便将工作件安全地夹住。
此外,夹紧表面应允许工具和夹具之间间隙以进行任何切割
特征
1.如果可能,通过设计工作件一侧的所有功能,最大限度地减少所需的设置数量
2.设计功能,如孔和螺纹,需要标准尺寸的工具
3.最小化所需的工具数量
4.确保任何功能的深度小于工具长度,从而避免与工作件接触
5.尽可能降低耐受性和表面粗糙度要求,以降低成本
6.设计内部垂直边缘,使角半径等于标准工具。如果必须安装具有外部锐利边缘的另一个组件,则钻一个孔以提供救济区域
7.避免非常长和薄的功能
8.使用 chamfer 而不是外部水平边缘的角半径
9.避免下切
成本驱动程序
材料成本
材料成本由所需的材料库存数量和该库存的单价决定。库存量由工作件大小、库存大小、库存削减方法和生产数量决定。材料库存的单价受材料和工作件形状的影响。此外,任何因从库存中切割工作件而产生的成本也会导致总材料成本。
生产成本
生产成本是总生产时间和小时费率的结果。生产时间包括设置时间、负载时间、切割时间、空闲时间和工具更换时间。减少这些时间组件中的任何一个将降低成本。设置时间和负载时间取决于操作员的技能。然而,削减时间取决于许多因素,影响削减长度和饲料率。通过优化所需的操作数量并尽可能缩小功能大小,可以缩短切割长度。进给率受操作类型、工作件材料、工具材料、工具大小和各种切割参数(如切割轴向深度)的影响。最后,工具更换时间是有关工具成本的讨论工具更换次数的直接结果。
模样成本
加工的工具成本取决于所需的切割工具总数和每个工具的单价。工具的数量取决于执行各种操作所需的独特工具数量以及每个工具所体验的磨损量。如果工具磨损超过工具的使用寿命,则必须购买替换工具。工具的使用寿命取决于工具材料、切割速度等切割参数和总切割时间。工具的单价受工具类型、大小和材料的影响。
科理咨询拥有30年专业经验,长期服务于财富500强,专注于提升企业的改善与创新能力,为客户持续创造价值。凭借在流程管理领域的专业经验和技术积淀,与国际TRIZ协会(MATRIZ)、德国弗劳恩霍夫学会等30多家国际权威机构展开深度合作,致力于为中国制造业和服务业构建更为专业的持续改善与创新的智能平台。
科理咨询(深圳)股份有限公司
深圳市科技园南区高新园一道013号赋安科技大厦B座301室
电话:0755-26993418