一次设计变更引发的思考:
一家家电企业在一次开发新产品过程中,设计工程师在产品定型后,收到了市场反馈的客户新需求,就决定在产品上增加一个新的功能模块,由于产品的主框架已经确定,整体外形不能增大,这个模块就只能放在产品侧面一个仅有的空位上。然而,当产品的样机放到装配线上试装时,人们才发现,由于产线上的产品与产品之间间距太小,侧面增加的这个模块几乎无法在产线上安装。要想安装就需要在工位上增加一个可抬升和旋转的托盘,将产品旋转90度,再安装侧面这个新模块,然后再旋转回原位,才能继续后面的装配。显然,这个可旋转的托盘需要增加生产线的成本,也会影响产线的节拍时间。而造成这个问题的根源在于设计变更的过程,设计工程师与生产线人员缺乏有效的沟通,而且,设计变更给生产带来的成本增加也缺乏可靠的数据评估,潜在会造成一部分成本如生产成本增加。
有什么方法可以防止这种问题的发生呢?首先,重大的设计变更需要有一个审核流程管控,相关的各个部门包括研发、工艺、生产管理、采购等部门都应该参加,对于变更带来的影响,尤其是可制造性和产品成本的影响一定要做严格的评估,保证不会发生上述的低级错误;其次,对于变更会给相关成本带来的影响,需要有相应的明确的数据支持,而且,这个数据对于研发部门和生产工艺部门都应该是透明的。
其实,不仅是设计变更需要有与产品成本数据的支持,整个产品开发过程都应该有这样的数据支持,这样,才能把产品的成本从设计伊始就做到精准控制。如果要让这样的数据可以既支持到设计过程对产品成本的评估,又可以帮助生产工艺人员合理安排产线和工位,并准确评估生产成本。
现在,很多企业都希望能从开发阶段就控制好产品相关的各项成本,而且还常常要求各个相关部门在产品立项的时候就做出达成产品目标成本的承诺。由于新产品在开发早期还远未定型,如果缺乏合理的估算模型,以及部门间的合作方式,这种早期的承诺往往无法落到实处。而在所有产品开发相关成本中,产品生产成本可以说是最难在早期确认的。原因也很简单,在开发早期,如果连设计工程师都还没有确定产品的具体方案,生产人员又怎么能够确定生产线上的具体安排呢?所以,建立一个贯穿整个开发过程的产品成本数据模型就显得非常重要了。
产品开发阶段成本模型的构想:
这样的成本数据模型应该能够与产品结构直接对应,并且可以包含生产相关信息。所有的数据调整对于开发流程所涉及的各个部门都应该是透明的,以避免由于设计变更带来的前后衔接不畅,造成各种配合上的问题。
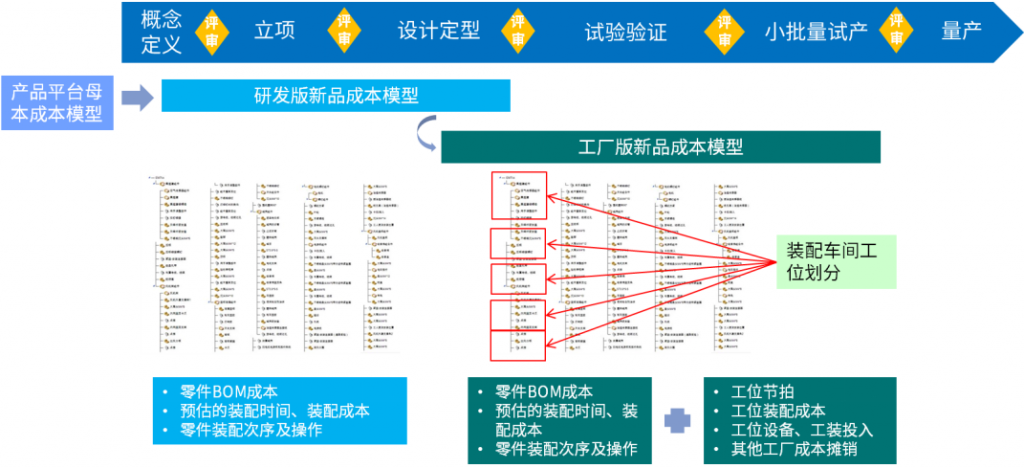
在图1中,产品从立项之初,就由研发人员根据现有的产品平台上的标准成本模型,初步确定产品的BOM成本,生成研发版新品成本模型。该模型可以采用DFMA®软件的产品结构图功能来完成。在此模型中,按照产品设计方案,产品包含的所有零件都按照装配次序从上到下排列好,并增加必要的装配操作。实际上,这样的数据体现了设计工程师对产品装配结构和操作的理解,不仅包含每个零件的BOM成本,也包含了对产品装配难度和时间的评估,进而包含了初步的装配成本。当设计定型后,这个成本模型就可以传递给生产工艺人员,经过他们的修改成为工厂版的新品成本模型。
与研发版相比,工厂版的成本模型又进一步增加了工厂的生产工位信息,因为每个装配工位所包含的装配步骤就不一定是设计工程师所设定的单一步骤,而会是某些步骤的组合。有了与工位对应的步骤组合,对装配成本的估算也就更加符合生产线的实际情况。同时,设备、工装的投入,以及工厂其他间接成本的摊销也都可以包括进来,这样,生产的成本投入就可以计算得非常清楚。更重要的是,当研发对设计方案进行变更时,就需要在研发版的成本模型上做相应的修改,而生产工艺人员要确认新设计方案的可制造性可以通过,就要按照设计变更修改工厂版的成本模型,并对实际产线进行评估,确保新的方案可以顺利在产线上实施。
以这种方式,产品成本数据对于整个研发过程涉及的各职能人员都是透明,从正向设计到设计变更,都高度数据化,对于所开发产品的成本的把控就可以做到既准确,又轻松。也为未来通过数字化平台管理产品全开发流程打下了坚实的数据基础。