在新产品开发的初始设计阶段运用DFMA®技术的好处是众所周知的,并且存在许多经典案例。不太为人所知的是,将DFMA®方法应用于已经接近生命周期末期的产品,也可以获得显著的收益。在以下案例中,DFMA®技术被用来重新设计全球数千种消费品中使用的电气连接器。这个简单的产品,只包含七个部件,由于成本压力,已经接近其生命周期的末期。通过应用DFMA®方法,产品以迭代的方式进行了重新设计,最终实现了产品的总成本降低了60%,从而使其使用寿命延长了许多年。
不仅产品的盈利能力得到了提高,而且使用DFMA®技术使泰科的设计团队能够经济有效地对设计进行一些细微的修改,使产品能够在新市场和应用中得以使用,从而进一步延长了产品的生命周期并提升了盈利能力。
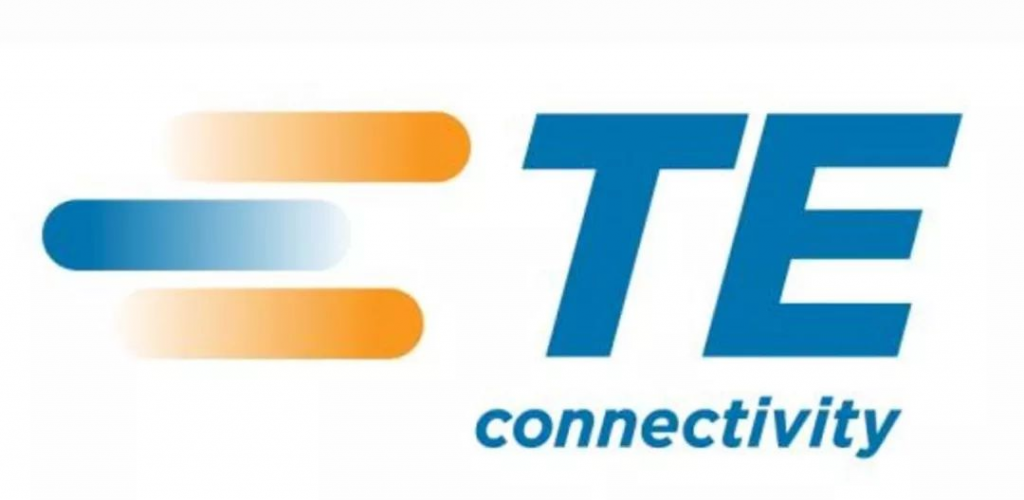
背景介绍
在本文将要介绍的案例中,泰科以与众不同的方式,将DFMA®方法应用于在DFMA®方法出现之前就开发出的一款老产品上。这款产品,一般称之为BNC连接器,是多年前为响应计算机网络工业的需要而开发的。
BNC连接器的设计是为了在用于将计算机联网的同轴电缆与计算机本身之间提供可分离的电气连接,因此,该产品已投入生产多年。近年来,由于BNC连接器比其他类型的电缆具有更优越的电气性能,因此它已被扩展使用到许多其它应用中。随着这一市场的扩张,随之而来的是成本的压力,以及如何将其扩展使用到全系列的所有相关产品上。当时,他们面临着一个商业挑战,即在产品生命周期的衰退阶段,评估什么样的市场反应是合适的?简单地说,他们有一个产品,在其预期的生命周期即将结束时,仍存在一个可有所作为的市场。
有没有什么流程或工具能使这个老产品”焕发新生”吗? 改善过程
这项工作的目标是尽快确定该产品的最低,且可实现的“成本”。从商业角度来看,他们认为可以选择以下三种业务策略中的一种。
1. 可以让产品逐渐退市,同时最大限度地获取他们可获得的利润。
2. 或者可以“迎接竞争”,重新定价(降价),以延长其生命周期到一个未知的时刻。
3. 或者可以以经济有效的方式增加产品特征,并通过开辟新的市场机会来延长产品的寿命。
如随后所见,他们选择了第三种策略。
为了应用DFMA®方法,他们首先必须确定适当的度量标准来判断设计决策的有效性。他们的利润是通过从市场价格和竞争对手为任何给定产品设定的价格中,减去他们的真实产品成本来确定的,所以他们必须确定自己的“成本”组成部分。他们称之为“总成本”概念。在他们的案例中,连接器的总成本由三个主要的综合经济变量决定,具体如下:
● 材料成本;
● 加工成本(即工具和加工过程相关成本);
● 组装成本。
① 材料成本的一阶决定因素是所用材料的类型和数量,以及加工过程中产生的废料数量。
② 加工成本的一阶决定因素(在他们的示例中,金属冲压、塑料注射成型和金属电镀)是所需加工工具的类型和数量;这些工具的复杂性反映在必须回收的工具资金成本及其安装和维护成本中;以及所需的部件加工周期时间。
③ 将原材料正确加工成成品部件,以备组装。组装成本的一阶决定因素是组装过程的类型(手动、半自动或全自动);组装设备的复杂性;组装周期时间;以及对二次操作的任何要求。
基于以上”总成本”概念,他们选择了使用一组可测量的DFMA®指标。经验告诉他们,做为评估标准,这些指标与他们的成本有直接的一对一关系。这就使得他们的财务人员投入项目的非增值时间最小化。因此,他们选择了四个测量指标进行研究。
1. 所需工具数量(加工和组装)
2. 工具的复杂性
3. 所需移动次数
4. 材料用量
再进一步解释,所需工具的数量产生了相应的资本投入,必须在产品的销售价格中进行摊销。工具的复杂性驱动了一系列成本,这些成本反映了单个工具成本、维护成本和安装成本。移动次数反映了整个制造过程的复杂性,从而反映了与特定的设计方案相关的制造周期时间。最后, 材料用量直接关系到他们作为成品出货的金额,以及进入废料堆的金额(也必须分摊到产品成本中)。
这项DFMA®工作由一位主任工程师负责,还有另外一位设计工程师,他们都是项目的全职设计工程师。该团队还根据需要配备了几位熟悉不同阶段制造过程的工艺工程师、材料工程师、财务人员和代表“客户之声”的产品管理人员。
对照“手动精密部件组装的DFMA®指南”和“高速精密部件组装的DFMA®指南”(请参见附录), 该团队启动了对现有设计和备选新设计的评估。这一看似矛盾的评估是必要的,因为他们知道许多客户希望“本地采购”,这就需要低成本、劳动密集型的手工组装;而其他客户产量大,从而需要高速、低手工劳动占比的自动化机器组装。
改善效果
最初的产品设计需要塑料和金属部件的组合,这需要大量的紧固件和紧固操作,以及在组装过程中的许多重新定位。它还要求使用几个仅适用于小批量操作的加工过程,因此,在最终组装之前,需要进行二次操作来检查和修理部件。众所周知,在他们的行业中,塑料注射成型技术具有明显的优势,因为一个塑料部件通常可以设计为替代几个金属部件及其相关的组装操作。因此,团队的第一项活动就是尽可能地将设计转换为全塑性设计,并且利用尽可能多的卡扣来紧固组件。
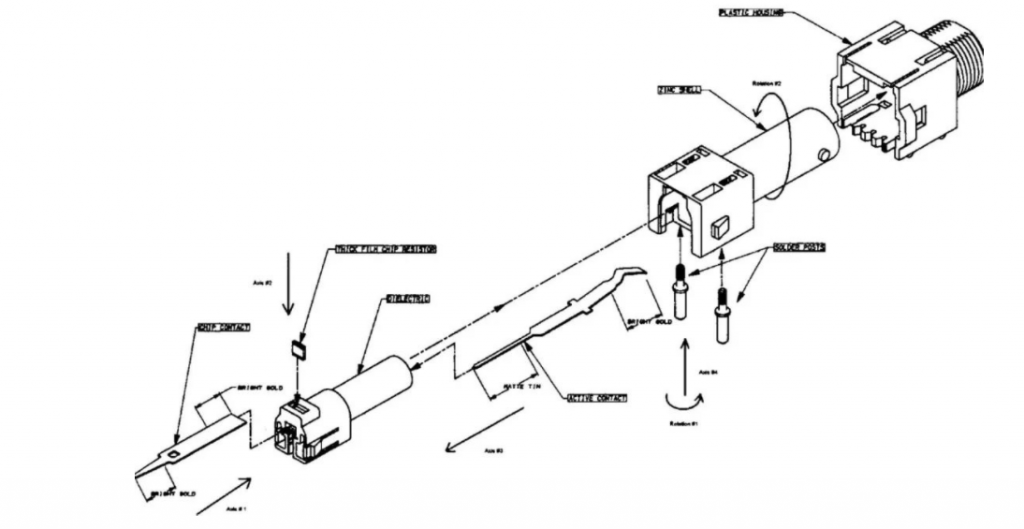
根据DFMA®准则,基准设计中的几个差异非常明显。第一个是完成组装所需的移动次数。需要在四个方向上进行横向移动或重新定位,并且至少需要两个旋转对准和一个螺钉紧固操作。使这种情况复杂化的是,缺少正确定位组件所需的适当对称条件,并且无法对设计进行分层。
该团队立即开始根据DFMA®指南有条理地进行设计评估,每次都改变有限数量的变量,以评估加工和组装组件的替代方法的影响。如下表,设计指标迭代比较显示了三个迭代设计的结果。请注意,参考设计是成本最高的现有(原)设计,所有其他备选设计的指标都是按照原设计的指标现状按比例折算而来。
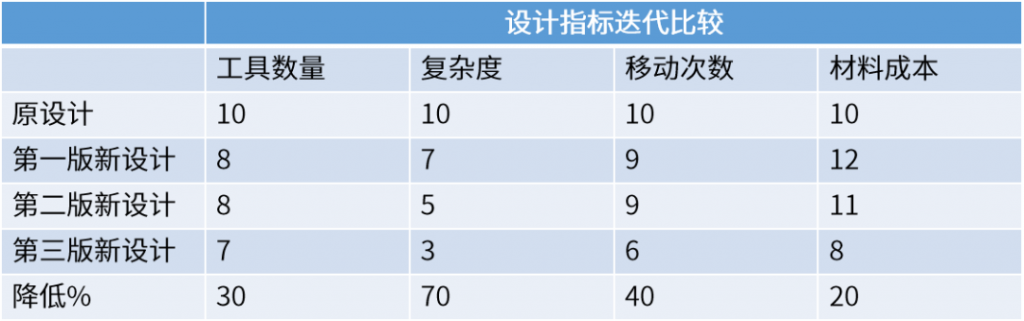
在第一次迭代中,对设计进行了修改,主要是两个触点从同一个面组装到电介质中(规则M7和A7)。有趣的是,所需工具的数量减少了,组装设备的复杂性也降低了,但零件成本却上升了!这主要是由于为了与重新设计的部件的复杂性相称, 成型电介质的成本上升。认识到这一事实后,该团队展开了第二个设计,重点是针对加工过程工具要求(规则M10和A8)来优化单个部件设计。
由于“总成本”概念是基于将工具能力与部件特征相匹配,团队认为“工具复杂性”指标的下降表明,在进一步调查组装过程之前,必须对单个部件进行优化。此活动的结果显示为上表中的“第二次”迭代。
这次迭代设计显著降低了工具的复杂性,但仍然没有实现适当的总体成本降低。第三次迭代的重点是使用新优化的组件组装过程。最后的迭代集中在三个重要的设计特性上。首先是在让塑料外壳具备适当的对称性,与卡扣配合一起,使其易于定向并插入分层设计中(规则M4、A2、A3和A5)。第二,重新设计了锌外壳,以便将原来分开的并拧入到位的支柱铸造到位。
这不仅消除了几个组装操作,而且还提供了适当的设计对称性和分层设计。最后,对主动触点进行了重新设计,以消除前边缘的复杂形状,因为它需要在制造过程进行检查(规则M3和M11)。此项迭代设计的结果为上表中的“第三次”迭代。 改善总结
团队通过第三次迭代达到了总成本目标,并且顺利投入量产。有趣的是,以往工程师们从传统思维的角度考虑降低精密部件的成本时,他们通常只考虑降低材料成本,因为它通常在产品成本的柏拉图分析中显示出很高的成本。在本案例研究中,实际的材料成本的减少幅度并不是最大的。相反,对该产品总成本的主要影响来自组装成本。这一事实强烈支持并验证了将DFMA®方法应用于所有产品的有效性和必要性。
如下表所示,从总成本上看,虽然第一次和第二次设计迭代在组装成本上产生了一些的节约,但第三次却产生了显著的节约。简单使用DFMA®准则,并确保所建议的设计符合这些准则,有助于生成具有稳健的制造过程和成本竞争力的设计。
从前面的讨论中并没有明显指出的是,这些设计活动还带来了额外的收益。他们不仅能够降低制造成本,从而提高竞争力,延长产品寿命;而且通过新的设计,他们能够在设计和组装过程中提供足够的灵活性,从而使多个部件可以互换以产生一系列电气性能的变化。这使得他们能够提供产品的“定制”版本,使用在许多其他应用中。这为曾经“垂死”的产品打开了许多新的市场。DFMA®方法的应用不仅延长了产品的寿命,而且为产品线提供了新的增长机会!
附录:
手工精密部件组装指南 (1)
M1:尽量减少部件数量。
M2:最小化部件类型的变化。
M3:消除过程中的调整和检查。
M4:提供部件的自对准、自定位和自紧固功能。
M5:确保有足够的空间让组装工具接近部件。
M6:提供适合“人工拿取”的散装包装部件。
M7:在组装过程中尽量减少重新定位的需要。
M8:防止组装错误。
M9:最大化部件的对称性。
M10:优化部件特征设计,以匹配工具的6西格玛能力。
M11:使部件的每个关键维度都可接近
高速精密部件组装指南 (1)
A1:确保部件可以在振动情况下运送进装配轨道。
A2:确保零件易于定向和/或可通过视觉系统识别。
A3:确保零件不需任何二次操作即可固定。
A4:提供自动校准功能。
A5:将所有产品设计分层。
A6:消除所有需要高插接力的放置操作。
A7:使用单一动作加工工具和单轴运动组装工具。
A8:优化组装特征设计以匹配组装设备的6西格玛能力
注:此处给出的指南是基于美国BDI公司的DFMA®指南,并对其进行了一些修改,以使其更适用于我们的行业。