注射成型是制造塑料零件最常用的制造工艺。使用注射成型技术制造的产品种类繁多,在尺寸、复杂性和应用方面差异很大。注塑工艺需要使用一台注塑机、原始塑料材料和一个模具。塑料在注塑机中融化,然后注入模具,在那里冷却并凝固成最终部件。下一节将更详细地描述这一过程中的各个步骤。

典型 | 可行的 | |
形状 | 薄壁圆柱形 薄壁方形 薄壁立方体复杂的 | 平坦 |
零件尺寸 | 信封。0.01英寸³ – 80英尺³ 重量:0.5盎司-55磅 | |
材料 | 热塑性塑料 | 复合材料 弹性体 热固性树脂 |
表面处理 – Ra: | 4 – 16 μin | 1 – 32 μin |
公差 | ± 0.008 in. | ± 0.002 in. |
最大壁厚 | 0.03 – 0.25英寸。 | 0.015 – 0.5英寸。 |
数量 | 10000 – 1000000 | 1000 – 1000000 |
交付时间 | 几个月 | 几个星期 |
优势 | 可以形成复杂的形状和精细的细节 优良的表面处理 良好的尺寸精度 生产率高 劳动成本低 废料可以回收利用 | |
劣势 | 只限于薄壁零件 工具和设备成本高 可能有较长的交货时间 | |
应用 | 壳体、容器、盖子、配件 |
注射成型被用来生产薄壁塑料零件,应用广泛,其中最常见的是塑料外壳。塑料外壳是一种薄壁外壳,通常需要在内部设置许多肋骨和凸台。这些外壳被用于各种产品,包括家用电器、消费电子、电动工具,以及作为汽车仪表板。其他常见的薄壁产品包括不同类型的开放式容器,如水桶。注塑也被用来生产一些日常用品,如牙刷或小型塑料玩具。许多医疗设备,包括阀门和注射器,也是用注塑法制造的。
注塑成型的工艺周期非常短,通常在2秒至2分钟之间,由以下四个阶段组成。
锁模 – 在将材料注入模具之前,必须首先通过锁模装置将两半模具牢牢关闭。每一半的模具被连接到注塑机上,其中一半被允许滑动。以液压为动力的锁模单元将两半模具推到一起,并施加足够的力量,使模具在注射材料的同时牢牢关闭。关闭和夹紧模具所需的时间取决于机器–较大的机器(夹紧力较大的机器)将需要更多的时间。这个时间可以从机器的干循环时间来估计。
注射 – 通常以颗粒形式存在的塑料原料被送入注塑机,并由注射单元向模具推进。在这一过程中,材料被热和压力融化。然后,熔化的塑料被快速地注入模具,压力的积聚使材料被包裹和固定。被注入的材料量被称为注射量。由于熔融塑料进入模具的流向复杂多变,因此很难准确计算出注射时间。然而,注射时间可以通过注射量、注射压力和注射功率来估计。
冷却 – 模具内的熔融塑料一旦与模具内表面接触,就开始冷却。随着塑料的冷却,它将凝固成所需部件的形状。然而,在冷却过程中,零件可能会发生一些收缩。注射阶段的材料包装允许额外的材料流入模具并减少可见的收缩量。在所需的冷却时间过去之前,不能打开模具。冷却时间可以从塑料的几个热力学特性和零件的最大壁厚来估计。
顶出 – 在经过足够的时间后,冷却的零件可由顶出系统从模具中顶出,顶出系统连接到模具的后半部分。当模具被打开时,一个机构被用来将零件从模具中推出。由于在冷却过程中,零件会收缩并粘附在模具上,因此必须施加力才能将零件弹出。为了便于零件的弹出,在注射材料之前,可以在模腔的表面喷上脱模剂。打开模具和弹出零件所需的时间可以根据机器的干循环时间来估计,并应包括零件从模具中脱落的时间。一旦零件被顶出,就可以将模具夹住,以便进行下一次的注射。
注塑周期结束后,通常需要进行一些后处理。在冷却过程中,模具通道中的材料会凝固在零件上。这些多余的材料,以及任何已经发生的飞边,必须从部件上修剪下来,通常是通过使用切割机。对于某些类型的材料,如热塑性塑料,这种修剪产生的废料可以通过放入塑料研磨机(也称为再研磨机或造粒机)进行回收,将废料重新研磨成颗粒。由于材料特性的某些退化,再研磨物必须与原材料以适当的再研磨比例混合,以便在注塑过程中重新使用。
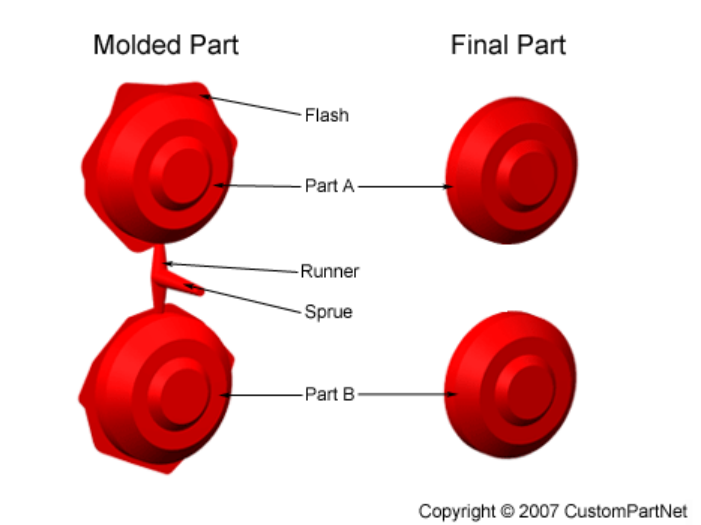
装备:注塑机有许多部件,有不同的配置,包括水平配置和垂直配置。然而,无论其设计如何,所有注塑机都利用动力源、注射单元、模具组件和锁模单元来完成工艺周期的四个阶段。
注射单元:注射单元负责加热和将材料注射到模具中。这个单元的第一部分是料斗,一个大容器,原料塑料被倒入其中。料斗有一个开放的底部,这使得材料可以进入料筒。桶内有加热和将材料注入模具的机构。这个机构通常是一个冲压式注射器或一个往复式螺杆。柱塞式注塑机通过一个通常由液压驱动的柱塞或活塞,迫使材料通过加热部分前进。今天,更常见的技术是使用一个往复式螺杆。往复式螺杆通过旋转和轴向滑动将材料向前移动,由液压或电动马达驱动。材料从料斗进入螺杆的凹槽,随着螺杆的旋转向模具推进。在推进过程中,材料在压力、摩擦和环绕往复式螺杆的附加加热器的作用下被熔化。然后,熔化的塑料在压力的积累和螺杆的前进作用下,通过料筒末端的喷嘴迅速注入模具。这种不断增加的压力使材料被包裹并强行固定在模具中。一旦材料在模具内凝固,螺杆就可以缩回,为下一次注射填充更多的材料。
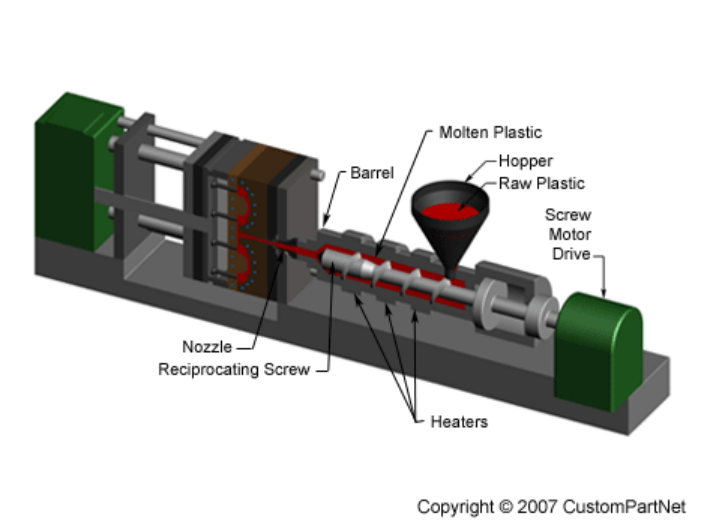
夹持单元:在将熔化的塑料注入模具之前,模具的两半必须首先由锁模装置牢牢关闭。当模具连接到注塑机上时,每一半都被固定在一块大板上,称为压板。模具的前半部分,称为模腔,安装在固定的压板上,并与注射单元的喷嘴对齐。模具的后半部分,称为模芯,安装在一个可移动的模板上,沿着拉杆滑动。以液压为动力的锁模马达驱动锁模杆,将可移动压板推向固定压板,并施加足够的力量,在材料注入和随后的冷却过程中保持模具的安全关闭。在所需的冷却时间过后,合模电机将模具打开。连接到模具后半部分的顶出系统由顶出杆驱动,将凝固的部件从开放的模腔中推出。
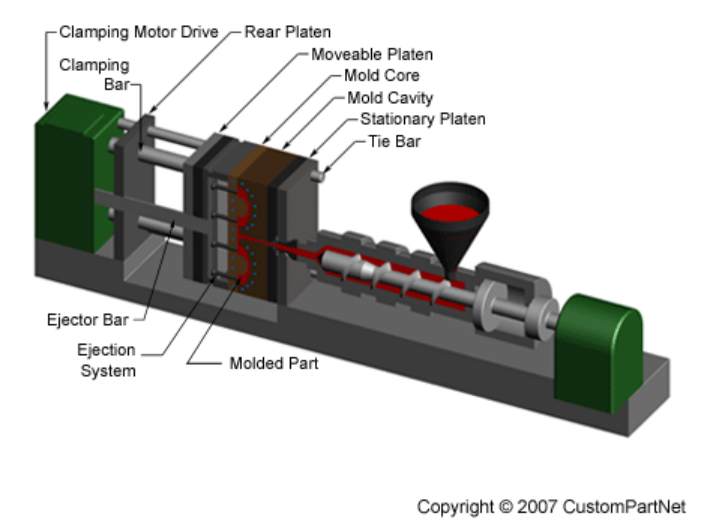
婴儿塑形器 | 权力线 | 寞子 | |
夹具力(吨) | 6.6 | 330 | 4400 |
射击容量(盎司) | 0.13 – 0.50 | 8 – 34 | 413 – 1054 |
夹具行程(英寸) | 4.33 | 23.6 | 133.8 |
最小模具厚度 (in.) | 1.18 | 7.9 | 31.5 |
压盘尺寸(英寸 | 2.95 x 2.95 | 40.55 x 40.55 | 122.0 x 106.3 |
机器规格:
注塑机通常以其提供的锁模力的吨位为特征。所需的锁模力是由模具中零件的投影面积和注射材料的压力决定的。因此,一个较大的零件需要较大的锁模力。此外,某些需要高注射压力的材料可能需要更高的吨位机器。零件的尺寸还必须符合其他机器的规格,如射出量、夹紧行程、最小模具厚度和压盘尺寸。
注塑件的尺寸可能差别很大,因此需要这些措施覆盖非常大的范围。因此,注塑机的设计是为了适应这一较大范围的数值中的一个小范围。以下是辛辛那提Milacron公司生产的三种不同型号(Babyplast、Powerline和Maxima)的注塑机的规格样本。

工具:注塑工艺使用模具,通常由钢或铝制成,作为定制的工具。模具有许多部件,但可以分成两半。每一半都连接在注塑机内,后半部分可以滑动,这样模具就可以沿着模具的分模线打开和关闭。模具的两个主要组成部分是模芯和模腔。当模具关闭时,模芯和模腔之间的空间就形成了零件腔,它将被熔化的塑料填满,形成所需的零件。有时也使用多模腔模具,其中两半模具形成几个相同的零件腔。
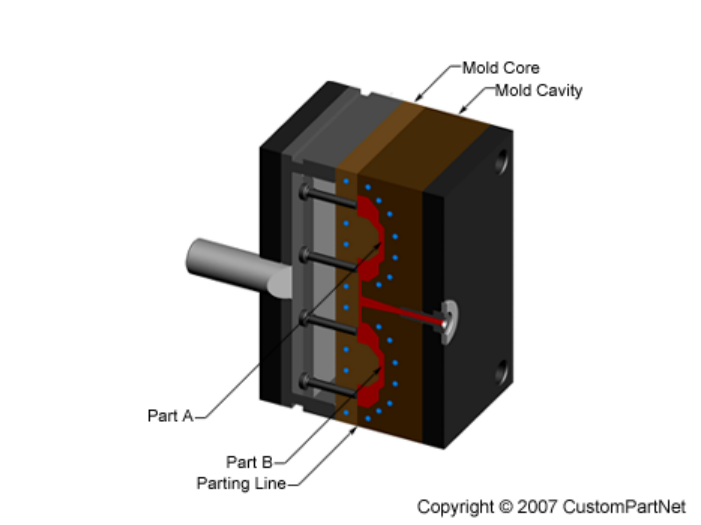
模具底座:模芯和模腔分别安装在模座上,然后固定在注塑机内的压板上。模座的前半部分包括一个支撑板,模腔与之相连;浇口套,材料将从喷嘴流入;以及一个定位环,以使模座与喷嘴对齐。模座的后半部分包括顶出系统,模芯连接在该系统上,以及一个支撑板。当锁模单元将两半模具分开时,顶出杆驱动顶出系统。顶出杆将顶出箱内的顶出板向前推,而顶出板又将顶出针推入成型件。顶出针将凝固的部件从开放的模具腔中推出。
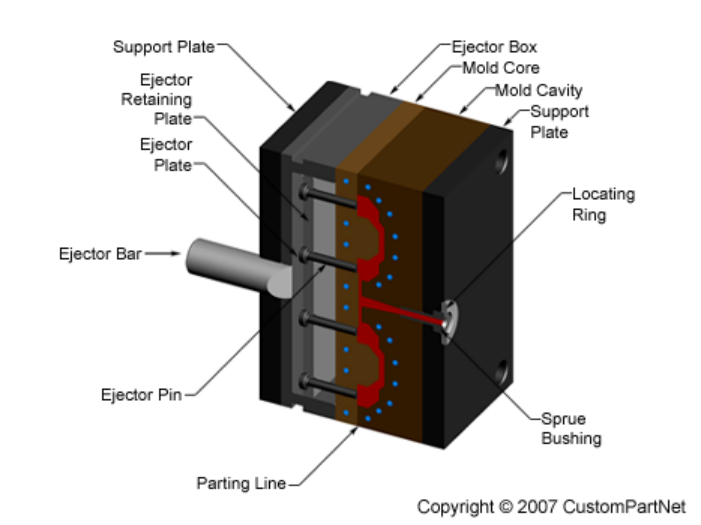
模具渠道:为了使熔融塑料流入模具型腔,在模具设计中集成了几个通道。首先,熔融塑料通过浇口进入模具。其他通道,称为流道,将熔融塑料从浇口输送到所有必须填充的型腔。在每个流道的末端,熔融塑料通过一个引导流动的浇口进入模腔。在这些流道内凝固的熔融塑料附着在零件上,在零件从模具中弹出后必须将其分离。然而,有时也使用热流道系统,该系统独立加热通道,使所含材料熔化并与零件分离。另一种内置在模具中的通道是冷却通道。这些通道允许水流过模具壁,与模腔相邻,并冷却熔化的塑料。

模具设计:除了流道和浇口外,在模具设计中还必须考虑许多其他设计问题。首先,模具必须允许熔化的塑料轻松地流入所有的模腔。同样重要的是将凝固的零件从模具中取出,因此必须在模具壁上设置一个拔模角。模具的设计还必须适应零件上的任何复杂特征,如底切或螺纹,这将需要额外的模具件。这些装置大多通过模具的侧面滑入零件腔,因此被称为滑块,或侧向作用。最常见的侧向动作是侧向模芯,它能使外部的底切成型。其他装置沿分模方向从模具末端进入,如内芯提升器,它可以形成内侧暗切。为了在零件中模塑螺纹,需要有一个脱模装置,它可以在螺纹形成后从模具中旋转出来。
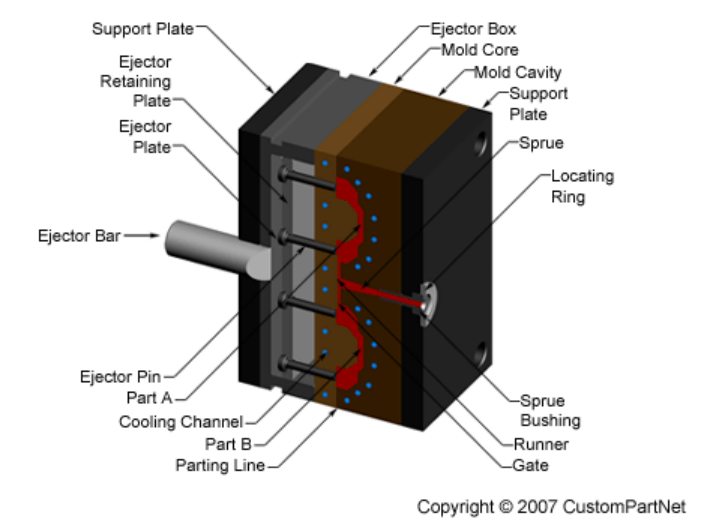
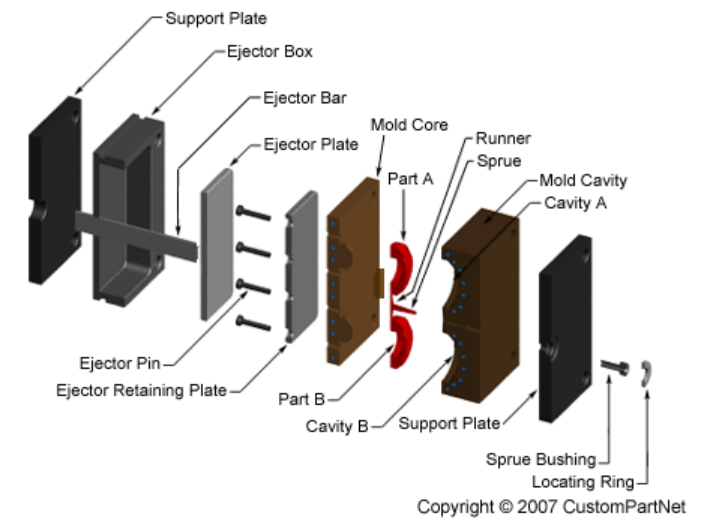
材料:有许多类型的材料可用于注射成型工艺。大多数聚合物都可以使用,包括所有热塑性塑料、一些热固性塑料和一些弹性体。当这些材料被用于注射成型工艺时,其原始形式通常是小颗粒或细粉。此外,在加工过程中还可以添加着色剂,以控制最终部件的颜色。选择用于制造注塑件的材料并不仅仅是基于最终部件的理想特性。虽然每种材料都有不同的特性,会影响最终部件的强度和功能,但这些特性也决定了加工这些材料时使用的参数。每种材料在注射成型过程中都需要一组不同的加工参数,包括注射温度、注射压力、模具温度、顶出温度和循环时间。
可能存在的缺陷:
缺陷 | 原因 |
闪光灯 | 注射压力过高钳制力太低 |
翘辫子 | 非均匀的冷却率 |
气泡 | 注射温度过高材料中的水分太多非均匀的冷却率 |
未填写的部分 | 射击量不足材料的流速太低 |
水槽标记 | 注射压力太低非均匀的冷却率 |
弹射器标记 | 冷却时间太短弹射力太高 |
上述许多缺陷都是由不均匀的冷却速率引起的。冷却速率的变化可能是由不均匀的壁厚或不均匀的模具温度造成的。
设计规则,最大壁厚:减少零件的最大壁厚,以缩短循环时间(特别是注射时间和冷却时间)并减少零件体积。
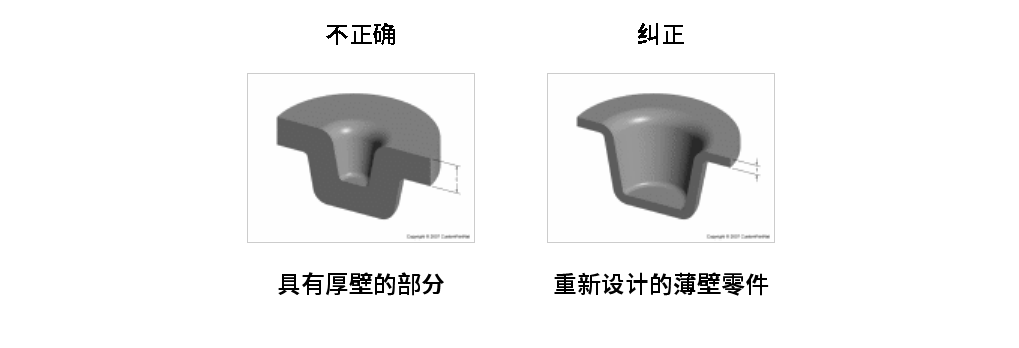
均匀的壁厚将确保均匀的冷却并减少缺陷
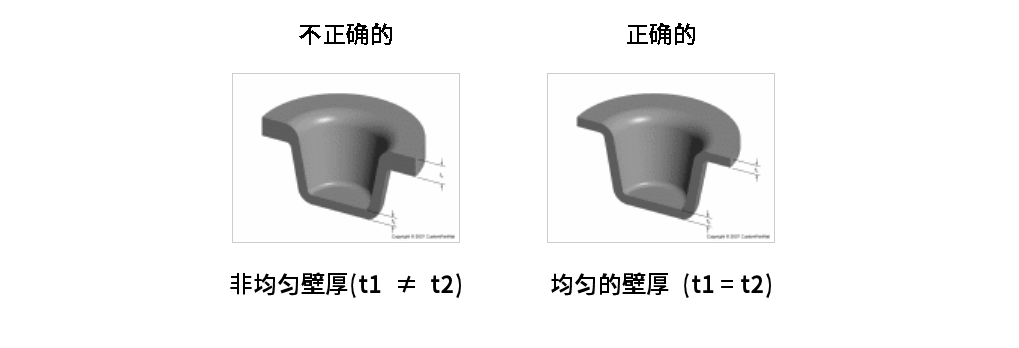
均匀的壁厚将确保均匀的冷却并减少缺陷
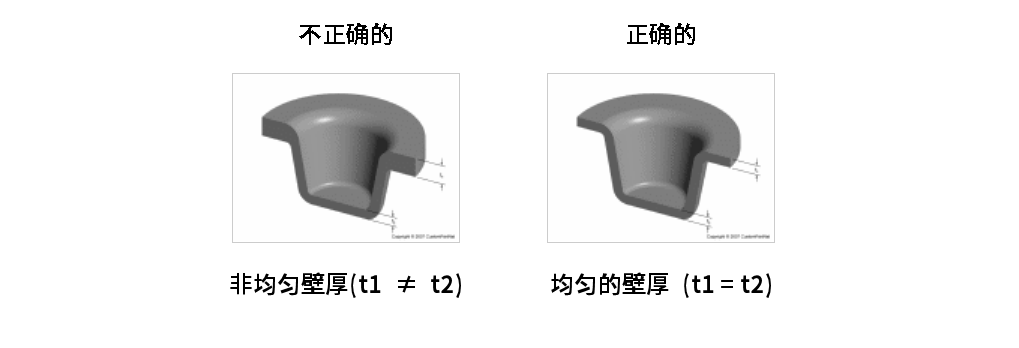
角落:圆角,以减少应力集中和断裂;内半径应至少是墙壁的厚度
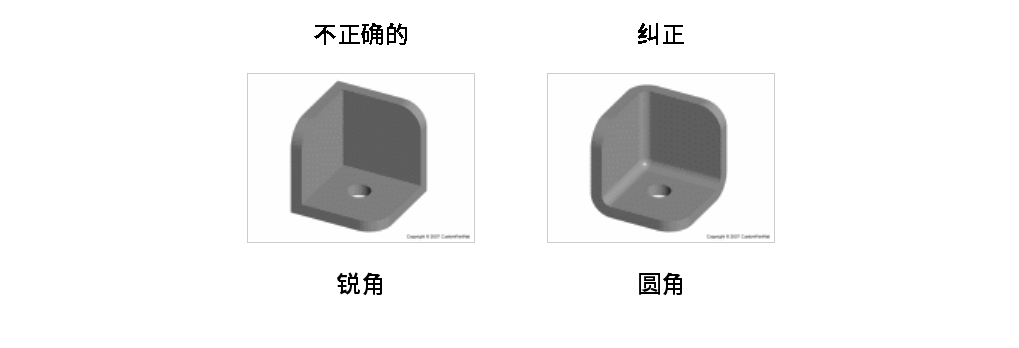
草案:在平行于分模方向的所有壁上施加1°-2°的拔模角,以方便从模具中取出零件。
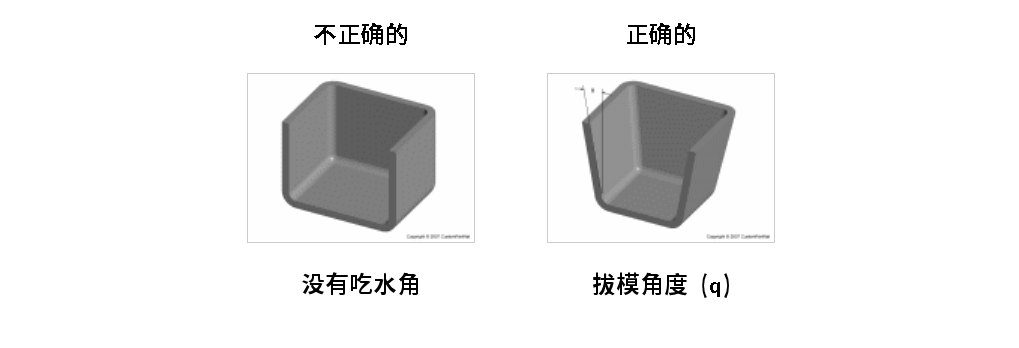
肋骨:增加肋骨作为结构支撑,而不是增加壁厚
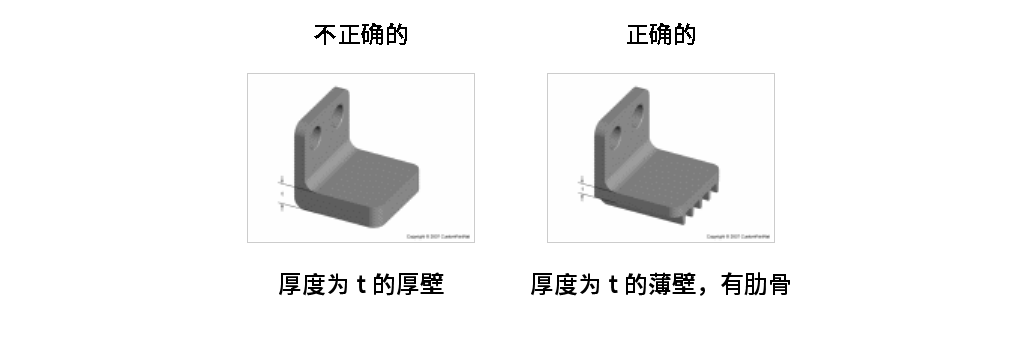
肋骨垂直于可能发生弯曲的轴线。
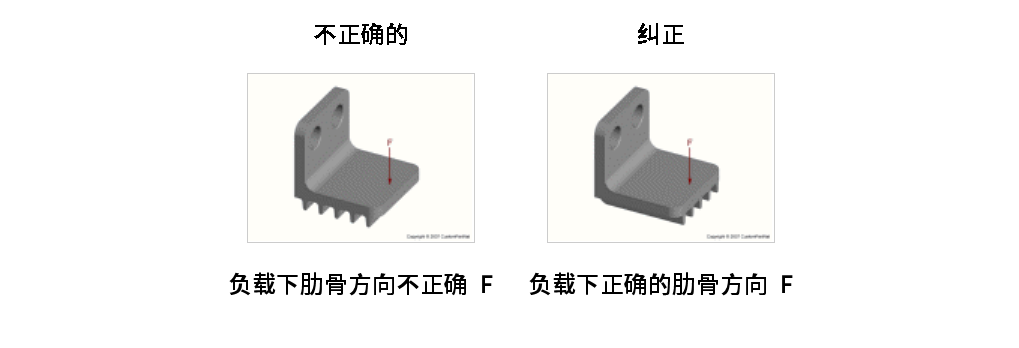
1.肋骨的厚度应该是它们所连接的墙壁的50-60%。
2.肋骨的高度应小于壁厚的三倍
3.在连接点上圆角
4.应用至少0.25°的拔模角
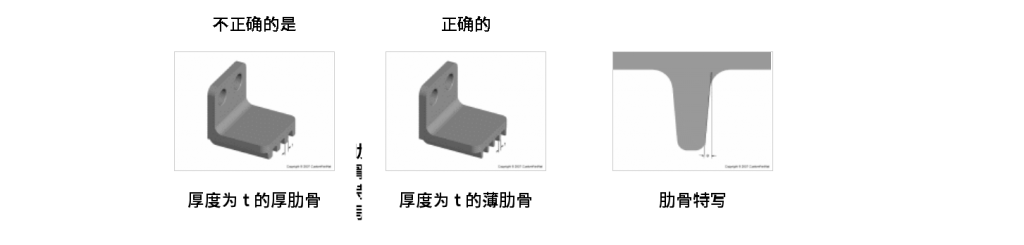
1.凸台的壁厚应不超过主壁厚的60%。
2.底部的半径应至少是主壁厚的25%。
3.应通过与相邻墙体连接的肋骨或底部的桁架来支撑。
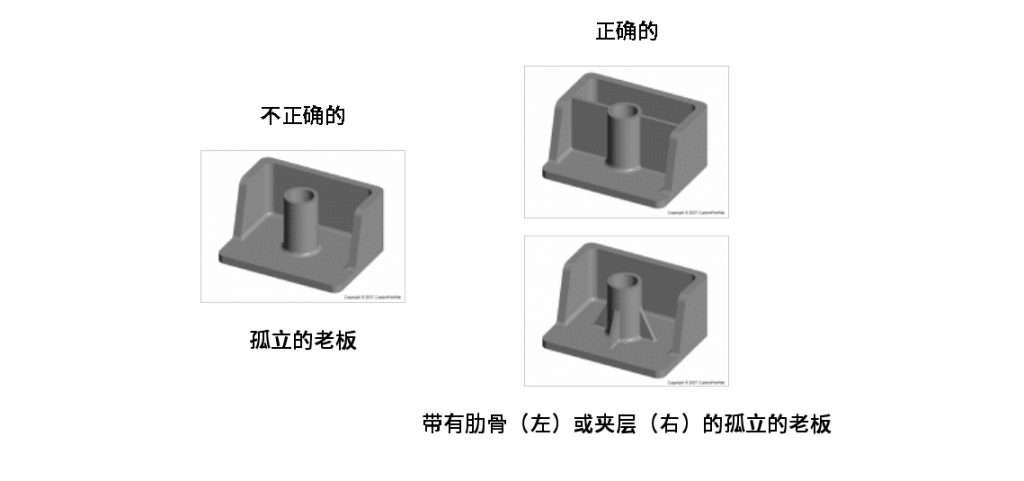
如果一个老板必须放在靠近角落的地方,应该用肋骨将其隔离。
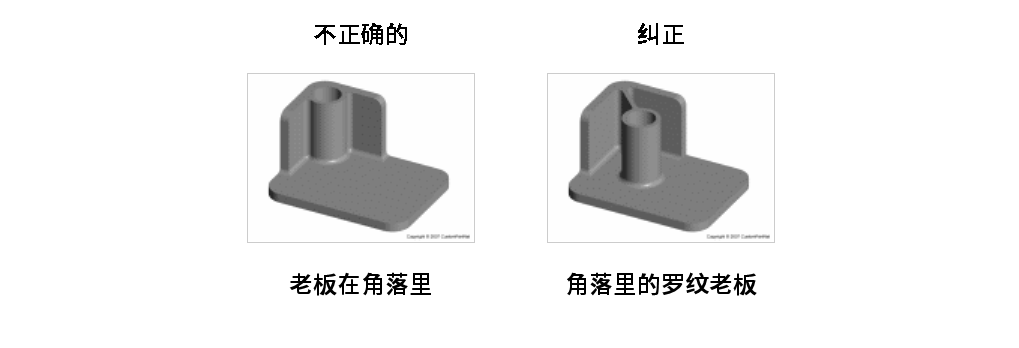
底部切口:
1.最大限度地减少外部切口的数量
2.外切需要侧切,增加了模具成本
3.一些简单的外侧下切可以通过重新定位分模线来成型。
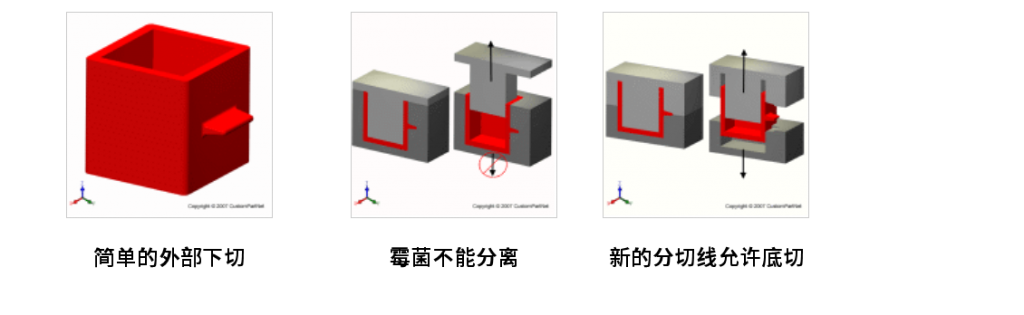
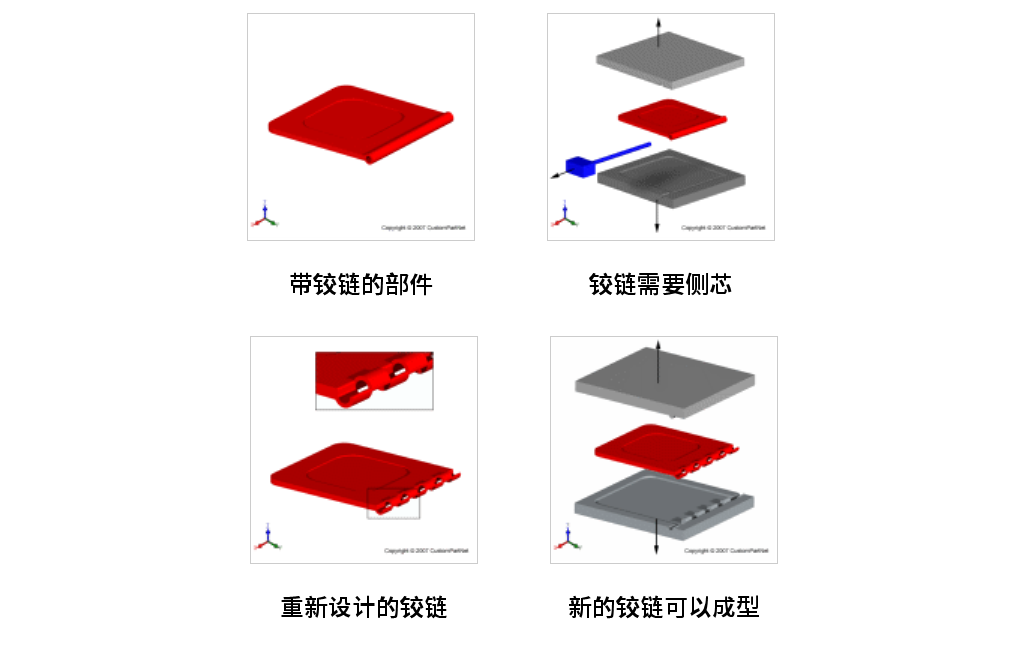
重新设计一个特征可以消除外部的暗切面
1.最大限度地减少内部切口的数量
2.内部开槽通常需要内部取芯器,这增加了模具成本
3.在零件的侧面设计一个开口,可以让侧芯形成一个内部的下切面
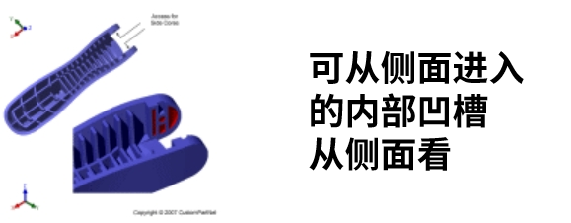
重新设计一个零件可以去掉内部的凹槽
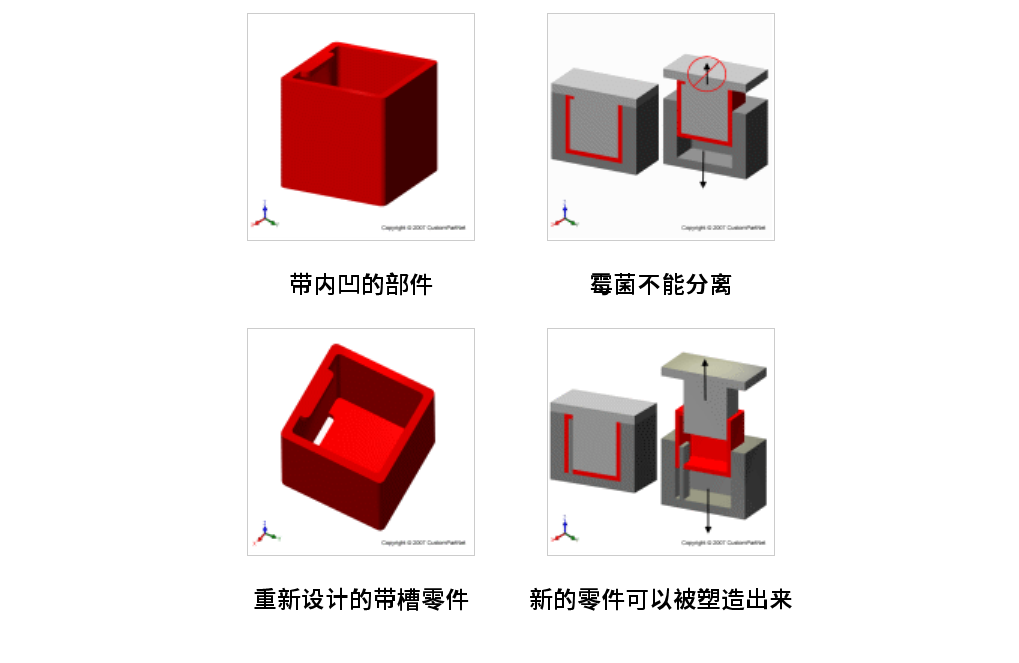
最大限度地减少侧面行动方向的数量
额外的侧面行动方向将限制模具中可能的型腔数量
缝纫机:
如果可能的话,有外螺纹的特征应垂直于分切方向。
与分模方向平行的螺纹特征将需要一个解旋装置,这大大增加了模具成本。
成本驱动因素
材料成本
材料成本是由所需材料的重量和该材料的单价决定的。材料的重量显然是零件体积和材料密度的结果;然而,零件的最大壁厚也会起作用。所需材料的重量包括填充在模具通道内的材料。这些通道的大小,以及由此产生的材料数量,在很大程度上由零件的厚度决定。
生产成本
生产成本主要由每小时费率和周期时间来计算。每小时费率与所使用的注塑机的大小成正比,因此,了解零件设计如何影响机器的选择非常重要。注塑机通常以其提供的锁模力的吨位来表示。所需的锁模力是由零件的投影面积和注射材料的压力决定的。因此,更大的零件需要更大的锁模力,因此需要更昂贵的机器。此外,某些需要高注射压力的材料可能需要较高吨位的机器。零件的尺寸还必须符合其他机器的规格,如夹钳行程、压盘尺寸和注射容量。
循环时间可以细分为注射时间、冷却时间和重新设定时间。通过减少这些时间中的任何一个,生产成本就会降低。注射时间可以通过减少零件的最大壁厚和零件体积来减少。对于较低的壁厚,冷却时间也会减少,因为它们需要较少的时间来全部冷却。材料的一些热力学特性也会影响冷却时间。最后,复位时间取决于机器尺寸和零件尺寸。一个较大的零件将需要机器做出较大的动作来打开、关闭和弹出零件,而较大的机器需要更多的时间来执行这些操作。
模具费用
模具成本有两个主要部分 – 模座和型腔的加工。模座的成本主要由零件包络的尺寸控制。一个更大的零件需要一个更大、更昂贵的模架。型腔加工的成本几乎受零件几何形状的各个方面影响。主要的成本驱动因素是必须加工的型腔的大小,由型腔的投影面积(等于零件的投影面积和投影孔)及其深度来衡量。任何需要额外加工时间的其他要素都会增加成本,包括特征数、分型面、侧壁、提升器、解旋装置、公差和表面粗糙度。
零件的数量也会影响到模具的成本。更大的生产量将需要一个更高级别的模具,它不会很快磨损。更强的模具材料会导致更高的模具基础成本和更多的加工时间。
最后一个考虑因素是侧向动作的数量,这可以间接影响成本。侧模的额外成本由使用多少个决定。然而,方向的数量会限制模具中可包含的型腔数量。例如,一个需要3个侧向的零件,其模具只能包含2个型腔。没有直接的成本增加,但有可能使用更多的型腔可以进一步节省成本。
科理咨询拥有30年专业经验,长期服务于财富500强,专注于提升企业的改善与创新能力,为客户持续创造价值。凭借在流程管理领域的专业经验和技术积淀,与国际TRIZ协会(MATRIZ)、德国弗劳恩霍夫学会等30多家国际权威机构展开深度合作,致力于为中国制造业和服务业构建更为专业的持续改善与创新的智能平台。
科理咨询(深圳)股份有限公司
深圳市科技园南区高新园一道013号赋安科技大厦B座301室
电话:0755-26993418