什么是IATF16949?
汽车行业最广泛使用的质量管理国际标准之一ISO/TS16949,随着国际汽车工作组(IATF)发布新的全球行业标准而更新。这个最新版本是由代表北美的AIAG成员以前所未有的行业反馈和高度参与来编制的。
ISO/TS 16949汽车行业质量管理体系技术规范已成为汽车行业应用最广泛的国际标准之一,协调了全球汽车供应链中不同的评估和认证体系。
2016年10月3日,IATF 16949:2016由IATF发布,取代并取代了过去的ISO/TS16949,定义了汽车行业组织质量管理体系的要求。
IATF 16949与DFMA®和DFSS的关系
这个新版本的标准在汽车行业的术语和定义内,新增了29个术语和定义。
而这便包含了一些我们常用的方法论如面向装配的设计(DFA)、面向制造的设计(DFM )、面向制造和装配的设计(DFMA®)、六西格玛设计(DFSS)等等。
除此之外,IATF 16949于条文8.3.5.1要求需要有产品设计的防错方法的如DFSS,DFMA®和FTA的产品设计输出结果,用以验证和确认产品设计输入要求。
为何IATF 16949强调了DFMA®和DFSS?
汽车行业产生高风险,高成本产品和服务并受到行业要求的严格控制; 根据IATF 16949修订小组,这个标准的目标是质量管理体系的发展这提供了持续改进,强调缺陷预防,以及减少变异和供应链中的浪费。
而DFSS是一种系统化方法,工具和技术,其目标是使成产品稳健,以满足客户的期望,并且可以在六西格玛质量水平下生产。
DFSS所要求用CTQ导出设计参数和工艺参数、以实验设计塔建转移函数、以函数将产品表现优化和减少变异。
DFMA®则结合了两种方法, 面向制造的设计(DFM)优化产品设计使生产更容易,产量更高,质量更高; 面向装配的设计(DFA),这是优化设计以降低错误风险,降低成本并使其更容易组装。
DFMA®强调藉结构设计和工艺/材料的选择来减少部件数量和组装时间,由于减少了部件数量减少和人为处理,这亦可以帮助产品减少变异和预防缺陷。
因此,DFSS和DFMA®
是有效㔹助IATF 16949的设计目标,这也是为什么它强调了DFSS和DFMA®的原因。
如何在标准条文要求内应用DFMA®和DFSS?
由于针对DFMA®和DFSS的要求是落在条文8.3.5.1设计与开发输出 – 附加要求上,而这应以可根据设计输入要求进行验证和确认的方式表现。
要留意这里强调了对设计输入的验证和确认。
针对DFMA®的应用应主要针对产品单位成本、部件重量或制造周期时间的设计输入,在对设计优化后比较该等设计优化后的单位成本、部件重量或个别制造周期是否能满足设计输入的需求便可了。
针对DFSS的应用也相对直接,设计输入一般会以关键质量特性CTQ为主,在DFSS 项目后期本身便要求对CTQ表现进行验证(如进行DOE后,估算和模拟CTQ结果是否在可接受范围内)和确认(如小样试作和CTQ是否在可接受范围内)。
案例分享
DFSS 项目
一般来说,汽车换热器(即散热器)的目标是以最有效的方式排除发动机热量。在汽车散热器中,热流体是发动机冷却液,冷流体是通过车辆前面板进入的环境/冲压空气。
为了实现这种以有效的方式处理发动机热量并且帮助达到期望的燃料经济性目标,需要设计散热器以在变化的环境温度下将发动机冷却剂温度保持在最佳预定极限。但是,通常这都会解读为一定热应力下保持散热器的排气温度(也称为风扇鼓风温度)。
这项目的调查集中在汽车散热器的优化设计,该散热器能够满足冷却发动机的基本要求,在最佳燃料经济性下运行,使冷却液温度降低,并且保持发动机舱下的空气温度低于可用于维持发动机组件的耐用性和性能。
为了达到这目标,这项目以DFSS方式推进,将范围集中在散热器优化设计上,以稳健设计的原理,分析设计因子如水管数量、端口距离、水管直径、水管壁厚、翅片间距、翅片高度、翅片宽度、翅片厚度等的设定水平,并同时将噪声音子如环境气流温度和环境气流流量纳入研究范围。实验完成后,以蒙地卡罗模拟估算表现以验证设计输入、再以样机试验确认设计输入和客户要求能够得以满足。
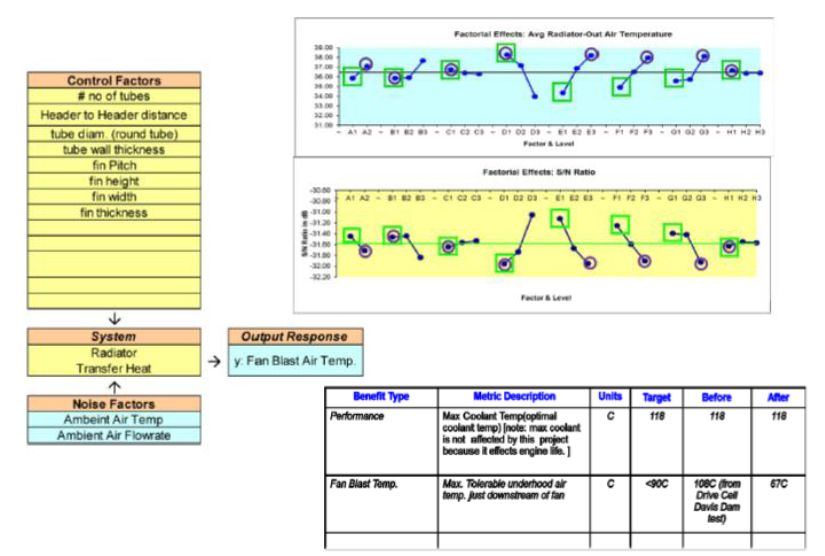
DFMA®案例
这案例是关于Magna皮卡的跳板。Magna工程公司被要求在大约8个月的时间内为北美市场设计和开发替代产品。关键问题是如何快速重新设计,维护特性和功能,并且仍然满足时序约束。
基线研究:DFA分析最初使用插图作为参考,然后分解实际装配。DFA基准的结果相当惊人;该组件由105个由四种基本材料类型组成的独立部件组成,使用多种不同的制造技术形成,并通过焊接,铆接,拧紧,咬合和模锻组装。
许多零件在组装件被切开之前都被隐藏起来,切开后露出多层材料,例如,插入管内的管子是由多件塑料子组件组成。
总计算装配时间超过1440秒,不包括涂料应用。制造了六个主要组件,许多小型件(小于25平方毫米)手工焊接到基本框架上,以便安装塑料装饰罩。 这可看到焊接被广泛应用。
另外,组装座椅底座支架就需要四次以上的重新定位。基本管状框架的组装需要插入很长的管,之后还要压平100mm长的部分并穿过15mm x 45mm的槽。在最后组装时,还有几个阻碍不便的操作。
使用基线分析的结果,对各种组件以合理化标准进行了低风险变更,通过与其他组件相结合来消除部件,并简化了处理和组装。合理性标准假定某些额外部件有一些充分的理由,并因应客户施加的时间限制给予一定的限制,从而限制额外新增的设计和开发工作,以满足工具加工日期的要求。
这个阶段的目标是保持座椅的所有基本功能,同时减少零件数量和装配时间。通过对相对较少数量的相关部件进行微小更改来合并或消除大量部件。
最重要的是,消除了大量的焊接步骤,特别是焊接焊工戴手套时很难或不可能处理的非常小的部件。通过略微增加材料的厚度以提供相同的性能,多层部件得到了加强。
凸轮和滚动部件更换为滑道并在狭槽中引导而不是形成导轨。由此产生的变化将零件数从105减少到19; 主要部件减少到5个,装配时间从1445秒减少到258秒。
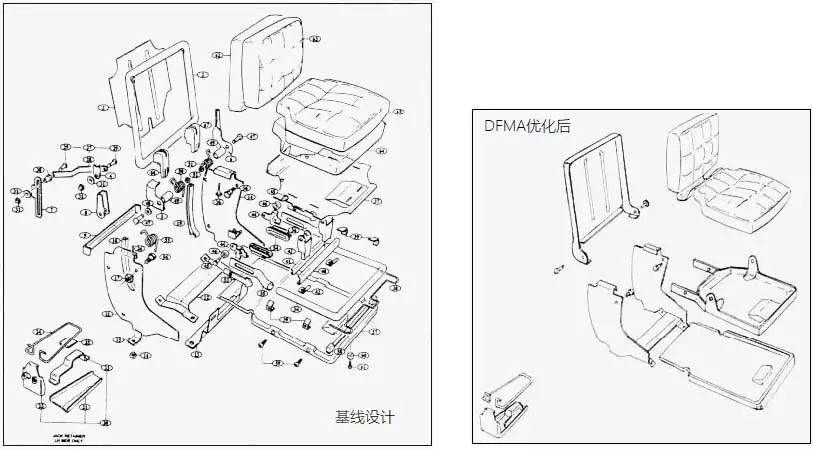
总结
从上述案例我们可以看到DFSS能有效将设计输出优化以确保其满足设计输入的要求,而DFMA®能有效将部件成本、重量和加工时间减少以确保其在成本方面和制造方面的设计输入要求。
当然,我们不能单单以工具的角度将它们插入到IATF 16949的质量管理体系内,而是要更有机的将它们融入到质量管理体系内,确保它们能有效帮助企业减少变异、预防缺陷和提升质量。